Using Rithum to Optimize Multi-Channel Fulfillment and Dropshipping
In this article
9 minutes
- What Is Rithum?
- Rithum at a Glance
- Core Capabilities: Rithum Modules Explained
- Why Rithum Matters for Modern Commerce
- Use Case: A Dropshipping Brand Using Rithum
- Brands and Retailers Benefiting from Rithum
- Challenges to Be Aware Of
- How Rithum Compares to Other Platforms
- Where Cahoot Fits In
- Final Thoughts
- Frequently Asked Questions
Rithum isn’t just a rebrand, it’s a reinvention. Born from the merger of ChannelAdvisor, CommerceHub, and DSCO, Rithum is now one of the most powerful platforms for brands, retailers, and suppliers navigating the connected ecommerce world. According to Rithum’s CEO, the rebrand marks the beginning of a new era focused on innovation, growth, and supporting customers at every stage of their journey. With over $50 billion in GMV flowing through its pipelines annually, Rithum is quietly powering some of the world’s greatest brands, and making optimized consumer shopping journeys feel seamless.
If your ecommerce strategy includes multi-channel order fulfillment, dropshipping, and scalable growth, Rithum might be the platform you didn’t know you needed. Rithum supports businesses from the very beginning of their ecommerce journey, streamlining onboarding and initial setup to ensure a smooth start.
What Is Rithum?
Rithum is a multi-module platform focused on creating connected ecommerce experiences. It brings together marketing, commerce, delivery, and discovery into one scalable solution, helping brands and retailers operate more efficiently across marketplaces, DTC sites, retail media networks, and fulfillment channels. Rithum is designed to help launch, manage, and grow any type of ecommerce business, supporting the entire commerce operation from inventory management to multi-channel sales.
In other words, Rithum gives you the tools to grow sales, manage inventory, expand fulfillment, automate operations, and scale, all from a centralized command center. It’s built for the brands, retailers, and suppliers who want to stop juggling disconnected systems and finally integrate everything, supporting users every step of the way as they integrate their systems.
Rithum at a Glance
- Annual GMV: $50+ billion
- Order Volume: Over 400 million orders processed per year
- Products Listed: 2.4 billion+ SKUs across 420+ channels
- Customer Base: 40,000+ companies, including major global retailers and niche DTC brands
- Trusted by the industry’s leading retailers and brands: Rithum supports the growth and profitability of retailers and brands across the ecommerce ecosystem.
- Legacy: Combines the capabilities of ChannelAdvisor, CommerceHub, DSCO, Cadeera, and more
That’s not just a lot of scale, it’s a lot of trust. Rithum powers commerce infrastructure for companies ranging from Fortune 500 retailers to fast-growing ecommerce entrepreneurs. As the industry’s most trusted commerce platform, Rithum delivers comprehensive solutions for retailers and brands navigating today’s market challenges.
Core Capabilities: Rithum Modules Explained
Rithum’s strength lies in its modular architecture. Businesses can tap into one, two, or all four of the core modules depending on their needs. Rithum supports businesses at every step, whether they choose a single module or implement the full suite, ensuring a smooth progression through each stage of their journey.
1. Commerce Solutions
This is the backbone. Rithum enables sellers to list products across hundreds of marketplaces, websites, social platforms, and retail sites, streamlining data sync, inventory updates, and pricing strategies.
Whether it’s Amazon, Walmart, Target Plus, Zalando, or your own Shopify site, Rithum’s software lets you manage product listings from one place. You can push updates to every sales channel instantly and reduce the lag that costs time, money, and customers.
2. Marketing Solutions
Rithum helps brands drive performance across paid search, social ads, and retail media networks. Think: Google Shopping, Meta Ads, Instacart, Criteo, Roundel, CitrusAd, you name it.
You can create optimized campaigns directly inside Rithum’s platform and integrate with leading analytics tools to tie ad spend to order fulfillment and margin impact. This means tighter control over ROAS, and faster decisions on what’s working and what isn’t.
3. Delivery Solutions
Order fulfillment isn’t just about speed, it’s about flexibility. Rithum’s delivery solutions automate routing based on inventory availability, warehouse proximity, shipping method, and cost-efficiency. This includes direct-to-consumer fulfillment, third-party logistics (3PL), and dropshipping.
Even better, Rithum integrates with Amazon MCF (Multi-Channel Fulfillment), letting brands use Amazon’s fulfillment infrastructure for non-Amazon orders. This creates margin advantages without the overhead of managing your own warehouses (though it’s quite a bit more expensive than outsourcing to 3PLs).
4. Discovery Solutions
Using AI and behavioral data, Rithum identifies top-performing suppliers, curates catalogs for buyers, and matches brands with new retail partners. This is especially powerful for B2B marketplaces and dropship networks looking to expand their assortments strategically.
The goal? Help suppliers work smarter, not harder, and give buyers access to high-margin, in-demand products without wasting time.
Why Rithum Matters for Modern Commerce
Let’s face it: managing ecommerce operations across 10+ sales channels is chaos without a platform like Rithum. The industry’s top brands use Rithum to automate, integrate, and grow. Here’s how:
1. Unified Inventory Management
Forget spreadsheets. Rithum provides real-time inventory visibility across all your selling channels. This helps reduce stockouts, improve fill rates, and prevent costly overselling.
2. Streamlined Order Fulfillment
Orders from Amazon, Shopify, Walmart, and your DTC site all route through a single order management system. Rithum auto-selects the best fulfillment method, be it internal warehouse, dropship partner, or Amazon MCF.
3. Data-Driven Marketing
Tie your product data to your ad performance. Rithum’s platform ensures that your marketing campaigns reflect inventory levels, promotions, seasonal trends, and shipping timelines.
4. Optimized Margins at Scale
One of the most underrated advantages of using Rithum is margin optimization. By automating fulfillment and identifying cost-saving delivery solutions, you increase profit per unit while maintaining fast delivery speeds.
5. Powerful Integrations
Rithum offers prebuilt connections with all major ecommerce platforms, marketplaces, and ERPs. Whether you’re using NetSuite, BigCommerce, Adobe Commerce, or Salesforce Commerce Cloud, Rithum plays nicely in the sandbox.
Use Case: A Dropshipping Brand Using Rithum
Let’s walk through a simplified scenario:
1. A brand lists 10,000 SKUs using Rithum’s commerce solution.
2. Rithum syndicates those listings to Amazon, Walmart, and a DTC site.
3. Inventory levels sync across platforms in real-time.
4. Orders start coming in from all channels.
5. Rithum routes the orders to a mix of 3PL warehouses and dropship suppliers based on margin and speed.
6. The marketing team uses Rithum’s tools to launch ad campaigns based on best-sellers and restock timelines.
7. The operations team reviews delivery metrics and margin performance using Rithum’s dashboard.
8. The brand expands to a European marketplace, using Rithum’s localization features and supplier discovery module.
Rithum enables brands, retailers, and suppliers to work together seamlessly throughout the dropshipping process, ensuring efficient collaboration and smooth order fulfillment.
From listing to delivery, everything flows through one platform, Rithum, acting as the heartbeat of your dropshipping operation and keeping every part running smoothly.
Brands and Retailers Benefiting from Rithum
Retailers like Belk used Rithum to onboard over 500,000 SKUs in under 90 days, resulting in a 36% YoY increase in GMV. Similarly, brands like Superdry and Marks & Spencer have leaned on Rithum’s marketing automation and fulfillment capabilities to grow international sales and reduce channel friction.
For smaller companies, the appeal is just as strong. Rithum lets lean ecommerce teams punch above their weight, automating order fulfillment, syncing inventory, and scaling ad campaigns without adding headcount.
Challenges to Be Aware Of
No platform is perfect. Here are a few potential drawbacks:
- Complex Onboarding: Rithum’s capabilities are powerful, but not plug-and-play. Implementation often requires a dedicated team or integration partner.
- Cost Structure: After the ChannelAdvisor/CommerceHub merger, some users reported pricing increases of 4–7x. Smaller businesses may need to weigh the ROI carefully.
- Support Transition: With consolidation comes some turbulence. Support quality can vary depending on your plan, region, and internal rep.
Still, these challenges are manageable if you’re serious about long-term scale.
How Rithum Compares to Other Platforms
Platform
|
Strengths
|
Weaknesses
|
---|---|---|
Rithum
|
Unified commerce, delivery, marketing
|
Complex onboarding, premium cost
|
Zentail
|
Easy setup, automation
|
Fewer marketplaces supported
|
Feedonomics
|
Robust product feed optimization
|
Limited fulfillment capabilities
|
Skubana
|
Inventory automation
|
Light on marketing tools
|
Cahoot
|
Fastest fulfillment via P2P network, most profitable reverse logistics
|
Primarily focused on shipping/logistics
|
Rithum is ideal for businesses seeking an end-to-end platform that supports everything from product discovery to last-mile delivery, especially if those businesses operate across multiple sales channels and want to optimize every piece of the puzzle.
To see how Rithum can help your business, schedule a demo to view the platform in action and learn more about its features and benefits.
Where Cahoot Fits In
For ecommerce sellers using Rithum but seeking faster, more cost-efficient fulfillment, Cahoot can be a perfect complement. While Rithum automates order routing and marketplace connections, Cahoot offers peer-to-peer fulfillment with 1-day ground delivery coverage across the U.S., at rates that beat most traditional 3PLs.
By integrating Cahoot into the Rithum workflow, brands can unlock smarter delivery solutions that drive higher margins and better customer experiences.
Final Thoughts
Rithum is more than just a new name; it’s a new rhythm for ecommerce. By merging legacy giants like ChannelAdvisor and CommerceHub, the Rithum platform is enabling connected ecommerce experiences at scale. With modules for commerce, marketing, delivery, and supplier discovery, it empowers brands, retailers, and suppliers to build lasting commerce businesses. Rithum also offers valuable resources to support teams and foster community within the ecommerce ecosystem.
It’s not for the faint of heart. Implementation takes planning. Costs can add up. But for ecommerce teams aiming to automate, scale, and integrate across channels, Rithum delivers.
Whether you’re launching a DTC brand, scaling a supplier network, or operating as one of the world’s greatest brands, Rithum helps create the infrastructure needed to move at speed, sell with confidence, and thrive in a fragmented retail world. Users love the seamless experience and impressive results they achieve with Rithum.
Frequently Asked Questions
What is Rithum, and what companies is it built from?
Rithum is a connected ecommerce platform formed by merging ChannelAdvisor, CommerceHub, DSCO, and other technology providers. It supports global brands, retailers, and suppliers.
How does Rithum improve order fulfillment and delivery solutions?
Rithum automates order routing across warehouses, dropship suppliers, and Amazon MCF, helping companies optimize shipping speed, cost, and customer satisfaction.
Which types of businesses should use Rithum?
Rithum is best suited for ecommerce brands, retailers, and suppliers managing sales across multiple marketplaces who need scalable software for fulfillment, marketing, and inventory.
Does Rithum offer tools for marketing and retail media?
Yes, Rithum’s marketing solutions connect directly to platforms like Google, Meta, Instacart, and retail media networks, helping businesses drive optimized consumer shopping journeys.
How does Rithum help brands expand globally?
Rithum’s commerce and discovery modules allow brands to manage listings across 420+ channels, onboard new suppliers, and localize product data to grow into new markets efficiently.
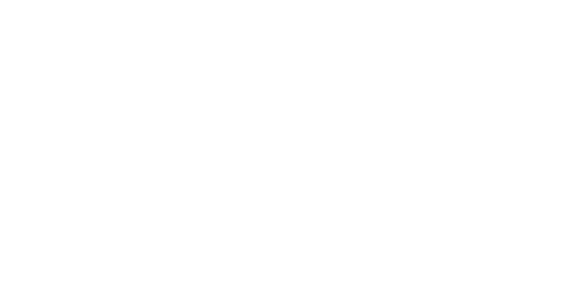
Turn Returns Into New Revenue
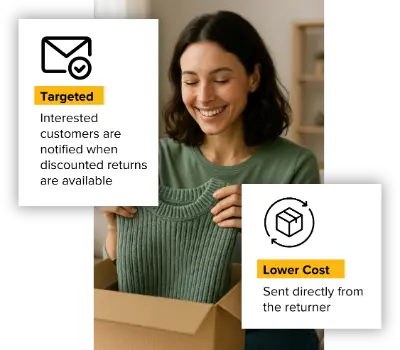
Faire: The Wholesale Marketplace Fueling B2B Retailers & Brands
In this article
9 minutes
- What Is Faire Marketplace?
- How Faire Works
- Why the Faire Marketplace Is Winning
- Inside the Faire Ecosystem
- Key Features That Power Faire Wholesale
- The Community Angle: Supporting Local Retailers
- How Faire Marketplace Stacks Up
- Challenges and Considerations
- Final Thoughts: A Smarter Way to Wholesale
- Frequently Asked Questions
If there’s one name shaking up the wholesale business right now, it’s Faire. This isn’t some old-school marketplace packed with overstock. Faire is modern, data-driven, and unapologetically pro-small business. The Faire marketplace connects brands with independent retailers, helps makers build loyal customer bases, and gives local retailers access to thousands of unique products at competitive wholesale prices, all without the traditional friction of trade shows, cold emails, or minimums that break the bank. The advantage for retailers and brands includes features like free returns, net payment terms, and exclusive access through membership programs, supporting small business success.
In short: Faire works because it flips the entire wholesale model on its head.
What Is Faire Marketplace?
At its core, Faire is an online wholesale marketplace built to help small businesses thrive. Retailers, particularly brick-and-mortar stores and local boutiques, use the platform to shop from hundreds of thousands of brands across the globe. These brands, in turn, use Faire to connect with eligible retailers in the U.S., Canada, Europe, and beyond, listing their products and managing everything from inventory to payment processing all in one place. Faire helps connect brands with local retailers through technology, building a community, and fostering relationships. The Faire site serves as the central hub for these transactions, and the website is the main online presence for wholesale activities.
Based in San Francisco, Faire was founded in 2017 with a bold mission: to level the playing field for local retailers and help independent brands find new audiences. Today, Faire wholesale is available in over 100 countries and supports a vibrant, rapidly growing ecosystem of retailers, makers, manufacturers, companies such as DTC brands and distributors, and wholesale suppliers. Faire connects brands and retailers around the world, creating a global community of buyers and sellers. The platform is also dedicated to supporting entrepreneurs and empowering small business owners with tools and market access.
How Faire Works
The platform operates like a matchmaking service between retailers and brands. Sellers create product listings, upload inventory, and set their wholesale prices. Retailers browse through categories ranging from home décor to beauty to food and drink, and place opening orders often backed by net 60 payment terms and free returns. Upon sign-up, retailers may be given a certain amount of credit or spending allowance, and after verification, may access additional credit limits. To access net payment terms, retailers need to verify their eligibility by linking their bank, point-of-sale, or accounting systems.
Here’s what happens behind the scenes:
- Product discovery is powered by machine learning, personalizing suggestions for each retailer based on store size, prior purchases, region, and even customer reviews.
- Opening orders often come with low minimums or free returns, removing the risk of testing new inventory.
- Payment processing is handled seamlessly, with sellers getting paid up front and retailers enjoying flexible terms. Retailers can pay using various methods, including credit cards, PayPal, Apple Pay, and benefit from net 60 or pay later options.
- Commission fees vary. Faire charges 15% on new retailer orders + $10, while Direct Orders (from returning buyers) are commission-free. A sale triggers payment and commission fees for the platform.
- Analytics tools help brands manage performance and optimize their listings, marketing campaigns, and reorder rates, providing actionable insights to both brands and retailers.
For retailers or brands considering alternatives to traditional fulfillment models, leveraging an order fulfillment network can maximize profits and efficiency.
Why the Faire Marketplace Is Winning
So, what’s different about Faire compared to traditional wholesale platforms or in-person markets? It’s the blend of tech, transparency, and trust.
First, brands retain control. Sellers manage pricing, inventory, fulfillment, and advertising through a clean, intuitive dashboard. With full visibility into order data, account trends, and customer reviews, they can fine-tune their approach like any modern ecommerce business.
Second, retailers get access to premium goods at wholesale prices without committing to large order volumes. That opens doors for thousands of local stores who previously couldn’t meet MOQs or navigate import logistics.
Third, Faire supports growth on both sides. Through powerful tools like email marketing, Facebook ad integrations, inventory syncing, and sales analytics, brands can grow their business while building meaningful relationships with independent retailers. Everyone wins. Faire helps brands reach more customers and grow their sales.
Inside the Faire Ecosystem
The numbers don’t lie:
- Over 100,000 brands now sell on Faire.
- Retailers have placed millions of orders from across Europe, Canada, and the U.S.
- In the UK alone, local retailers were offered 50% off first-time purchases and free delivery for eligible categories.
- Faire has raised over $1.29 billion in funding, giving it the backing to expand into more local communities and continue supporting small business growth.
And yes, Faire is one of Shopify‘s chosen partners, with a tight integration that helps Shopify sellers expand to wholesale with minimal friction.
Key Features That Power Faire Wholesale
Let’s break it down. These are the platform’s most compelling features for sellers and retailers:
1. Curated Product Listings by Category
Sellers categorize their items by vertical: apparel, wellness, home goods, kids, pets, and more. Retailers can filter by category, price, product type, margin, brand story, and more. The marketplace interface is designed to feel more like shopping a boutique than digging through bulk inventory.
2. Free Returns on Opening Orders
Risk is the biggest barrier for new buyers. Faire’s solution? Let retailers opt for free returns on opening orders, which removes the fear of testing unfamiliar brands. This is one of Faire’s most powerful conversion drivers and a huge incentive for local stores to experiment.
3. Real-Time Inventory and Order Management Tools
Brands can sync inventory with their own ecommerce store, receive alerts when stock is low, and auto-approve reorders from trusted accounts. Retailers benefit from instant updates on order status and fulfillment timelines.
4. Global Expansion with Localized Support
Sellers can target specific geographies like Canada or Europe with localized pricing, translations, and customer support. The platform handles currency conversions, tax calculations, and security. Faire’s San Francisco headquarters has expanded to offices in London, Amsterdam, and São Paulo.
5. Advertising and Marketing Tools
Using Faire’s built-in marketing suite, brands can create campaigns, retarget past buyers, and generate traffic from Facebook or Instagram directly from their dashboard. They can also opt into Faire’s promotional campaigns during key retail periods.
6. Direct Orders with No Commission Fees
Want to avoid platform commissions? Brands can invite existing wholesale buyers to their Faire storefront via a direct link, which lets both sides skip commission fees and still access Faire’s tools, tracking, and payment systems.
The Community Angle: Supporting Local Retailers
Faire isn’t just about wholesale, it’s about restoring the vibrancy of local shopping. By giving neighborhood retailers a chance to compete with big-box stores and letting consumers discover products that aren’t on Amazon or Walmart shelves, Faire helps communities thrive.
Independent retailers using the platform have reported higher margins, better product discovery, and faster turnaround than legacy wholesale options. From rural shopkeepers in Texas to boutique owners in Toronto, these small businesses now have global access without sacrificing their local flavor.
How Faire Marketplace Stacks Up
Feature
|
Faire Marketplace
|
Traditional Wholesale
|
---|---|---|
Free Returns
|
Yes (on opening orders)
|
Rare
|
Commission-Free Sales
|
Yes (via Direct Orders)
|
No
|
Built-in Analytics Tools
|
Yes
|
No
|
Global Retailer Access
|
100+ countries
|
Limited
|
Low Order Minimums
|
Yes
|
Usually high
|
Facebook Ad Integration
|
Yes
|
No
|
Payment Processing
|
Automated, flexible payout options
|
Manual or delayed
|
Challenges and Considerations
It’s not all sunshine and margins. Sellers must:
- Optimize listings and metadata to rise above hundreds of thousands of other brands.
- Adapt to algorithm changes that affect visibility and conversion rates.
- Accept that commission fees and advertising costs, while lower than trade shows, still add up over time.
Still, the advantages: speed to market, flexibility, insight, and buyer reach, are massive. Faire offers a variety of services to enhance user experience, from support to marketing tools. Users can review their privacy or cookie settings at any time and manage preferences by visiting the appropriate settings pages.
Final Thoughts: A Smarter Way to Wholesale
Whether you’re a U.S. candle maker, a Canadian ceramicist, or a European skincare brand, Faire helps create a smarter wholesale business. And if you’re a retailer? This is the platform that finally gives small stores the tools to compete. Makers and retailers can join the Faire marketplace by signing up and completing the onboarding process.
By combining product discovery, inventory control, analytics tools, payment processing, marketing campaigns, and customer relationship features into one elegant interface, Faire Wholesale has redefined the future of retail and made the playing field just a little more fair. Brands are encouraged to explore both selling on Faire Marketplace and their own wholesale store to maximize reach and sales opportunities, considering the benefits and limitations of each selling channel.
Frequently Asked Questions
What is the Faire marketplace, and how does it work?
The Faire marketplace is an online wholesale platform that connects independent retailers with brands and makers, offering access to curated products at wholesale prices.
Who can sell on Faire, and what are the commission fees?
Brands and manufacturers can sell on Faire. The platform charges a 15% commission on new retailer orders and $10 per opening order, but returning buyer orders are commission-free via direct links.
Are there minimum order quantities for retailers on Faire?
Faire allows flexible opening orders, often with low or no minimums. Retailers can try new products with reduced risk, and most first orders come with free returns.
What kind of products and categories are available on Faire?
Faire offers hundreds of thousands of product listings across categories like home décor, beauty, wellness, fashion, food and beverage, and more; ideal for boutique-style shops.
Can international retailers use Faire wholesale?
Yes, Faire supports retailers in over 100 countries including Canada and Europe, with localized currency, shipping, and payment processing.
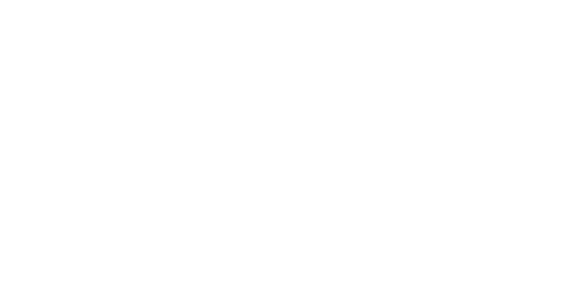
Turn Returns Into New Revenue
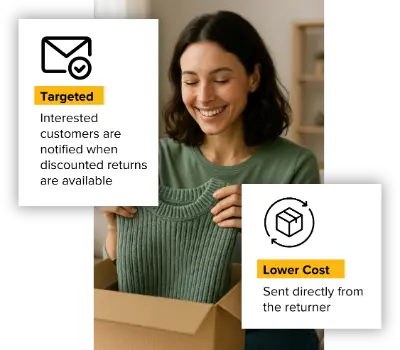
Cahoot vs Veeqo: A Value-Driven Comparison for Modern Ecommerce Sellers
In this article
9 minutes
- At a Glance: Cahoot vs Veeqo
- Pricing Models & Carrier Rates
- Order Routing & Workflow Automation
- Multi-Channel Capabilities
- Inventory & Warehouse Management
- Support & Learning Curve
- Amazon Buy Shipping & SFP
- Data You Can Actually Use
- Built for Amazon Sellers, but Not Owned by Amazon
- Pros & Cons
- Cahoot vs. Veeqo: What Sellers Are Saying
- Final Verdict
- Frequently Asked Questions
When ecommerce sellers start scaling across marketplaces like Amazon, eBay, Walmart, and Shopify, their shipping software can either accelerate that growth or slow them down. Two platforms built to handle multi-channel shipping are Veeqo and Cahoot. Both offer discounted shipping labels and order management tools, but the similarities end there. This in-depth comparison will explore what each software delivers, what it lacks, and which one ultimately supports fast-moving ecommerce teams better.
At a Glance: Cahoot vs Veeqo
Feature
|
Cahoot
|
Veeqo
|
---|---|---|
Multi-Channel Order Import
|
Yes
|
Yes
|
Discounted Carrier Rates
|
Yes
|
Yes
|
Rate Shopping Across Carriers
|
Yes
(Autonomous) |
Yes
(Basic) |
Bulk Label Printing
|
Yes
(Autonomous) |
Yes
(Traditional) |
Support for Own Carrier Accounts
|
Yes
|
Yes
|
Automation Rules & Order Routing
|
Yes
(Highly Configurable) |
Limited to Presets
|
Intelligent Package Selection (Cartonization)
|
Yes (AI-powered)
|
No
|
WMS Features
|
Yes
|
Partial
|
Inventory Visibility
|
Yes
(real-time) |
Yes
(limited granularity) |
Returns Workflow Integration
|
Optional Peer-to-Peer Returns
|
Basic RMA
|
Live Customer Support
|
Yes
(Help Desk, Phone) |
No phone support
|
Amazon Buy Shipping API Certified
|
Yes
|
Yes
|
Supports Amazon SFP
|
Yes
|
No
|
Open to 3PLs
|
Yes
|
No
|
Pricing Models & Carrier Rates
Both Cahoot and Veeqo offer access to discounted shipping rates from major carriers like UPS, FedEx, and USPS. Veeqo highlights its access to Amazon-negotiated carrier rates, especially beneficial for FBM sellers. However, it’s worth noting that Cahoot also offers deeply discounted rates through its aggregated carrier network, and unlike Veeqo, sellers aren’t required to be Amazon merchants to access them.
Users have praised Veeqo’s rates in particular, though some feel that the real-world savings depend on volume and location. One user on Trustpilot noted, “Veeqo offers good rates, but it doesn’t always beat what I negotiated directly with FedEx.” That said, having an option for both Veeqo and using your own account provides flexibility.
Cahoot lets sellers compare real-time rates across carriers, or even better: automate all the rate shipping and bulk shipping label generation based on the desired logic (cheapest, fastest, delivery promise, signature-required, etc.). This level of autonomous support (removing the human) goes a step further than Veeqo’s more manual workflows.
Order Routing & Workflow Automation
This is where the gap between the two platforms widens. Cahoot excels at automation.
Cahoot’s rule engine lets sellers automatically assign orders to specific warehouses, select packaging based on product dimensions, and pick carriers based on dynamic rules. It includes AI-powered cartonization, reducing overpackaging and optimizing label selection at scale. This feature alone can save high-volume shippers thousands per month.
Veeqo supports some automation, but according to multiple reviews, the rules engine lacks flexibility. As one user put it: “You can automate some parts of the shipping process, but complex routing logic just isn’t possible.” Another noted on G2, “Our warehouse team constantly has to manually override presets in Veeqo to get the right shipping option.”
Cahoot also offers the option to import product master data, assign SKUs to multiple warehouses, and automate routing for distributed fulfillment. These features are especially helpful for sellers managing multiple sales channels and warehouse locations.
Multi-Channel Capabilities
Both platforms support multi-channel order import from Amazon, eBay, Shopify, Walmart, Etsy, and more. Veeqo is tightly integrated with Amazon (it’s owned by Amazon), which brings advantages for FBM sellers, like access to Buy Shipping and automated order syncing.
However, some sellers note that Veeqo prioritizes Amazon workflows and that the support for non-Amazon channels lacks depth. A Trustpilot reviewer stated, “It’s clearly built with Amazon in mind. Shopify orders don’t always sync correctly, and the custom mapping is limited.”
Cahoot offers native integrations with all major ecommerce platforms, with equal priority across sales channels. That neutrality is useful for brands expanding beyond Amazon and looking to centralize operations across multiple storefronts.
It also means Cahoot isn’t limited by Amazon policy shifts or ecosystem changes. For businesses hoping to grow a multi-platform brand, that independence matters.
Inventory & Warehouse Management
Veeqo includes basic inventory tracking tools but doesn’t offer a full warehouse management system (WMS). Its UI shows available stock and syncs between platforms, but lacks pick/pack workflows, barcode scanning, and location-based inventory management.
Cahoot includes WMS features as part of the platform, with no need for third-party plugins. Sellers can assign bin locations, manage cycle counts, and generate pick lists automatically. One Cahoot user shared, “We reduced picking errors by 60% after switching from ShipStation to Cahoot because the WMS features are built in.”
For growing brands with even modest warehouse operations, this difference is key. It consolidates tech stack complexity and reduces reliance on disconnected tools.
Support & Learning Curve
Cahoot provides live onboarding, in-platform chat, and phone support. Multiple users note how responsive the support team is. One review on G2 says, “Every time I had an issue, Cahoot got back to me within minutes. I never felt like I was waiting around.”
Veeqo, on the other hand, has no phone support, and several users on Trustpilot and Reddit cite frustrating support delays. One review read, “You submit a ticket and wait… sometimes for days. It’s not great when your entire shipping flow is paused.”
Veeqo also has a steeper learning curve for non-Amazon users. The dashboard is robust but not intuitive for sellers focused on Shopify or direct-to-consumer models.
Amazon Buy Shipping & SFP
Both platforms are certified for Amazon Buy Shipping, meaning they help sellers remain compliant with Amazon’s policies and tracking requirements. However, only Cahoot supports Seller Fulfilled Prime (SFP).
For Amazon SFP sellers, this is a major differentiator. Cahoot’s compliance engine ensures same-day label printing, cut-off time enforcement, and late-delivery prevention. Veeqo does not support this, which rules it out for many brands trying to maintain the Prime badge.
Data You Can Actually Use
With Veeqo, many sellers are flying blind. Sales data is fragmented. Shipping costs aren’t always transparent. And pulling that data often means wrangling spreadsheets with missing headers or running into failed exports.
Cahoot makes it easy to analyze profits, understand shipping costs, and track eligible shipments in one dashboard. You get full access to real performance data without needing to bounce between platforms.
Built for Amazon Sellers, but Not Owned by Amazon
Veeqo is owned by Amazon. That means anything you do on the Amazon platform is potentially visible. For Amazon sellers trying to protect their strategy or operate across other channels, that’s a problem.
Cahoot is fully compatible with Amazon FBM, FBA, and Buy Shipping, but stays independent. You get the lowest rates available, without locking yourself in deeper with Amazon or giving up your leverage.
Pros & Cons
Cahoot vs. Veeqo: What Sellers Are Saying
“Using Veeqo costed us so much time. Exports kept failing, inventory didn’t match, and the UI was just confusing. Cahoot gave us back control.”
~ Multichannel seller, apparel industry
Speak to a fulfillment expert
“The only reason I stuck with Veeqo was because it was free. But once our shipping volume increased, we needed more, and Cahoot delivered.”
~ Electronics brand owner
Speak to a fulfillment expert
Final Verdict
Veeqo is a solid, free tool for Amazon-first sellers who want to print shipping labels and access decent rates with minimal setup. But it lacks depth in automation, support, and warehouse operations.
Cahoot, by contrast, is built for scale. It’s ideal for ecommerce brands that are serious about operational efficiency and growth. From smart automation to robust warehouse tools and superior customer support, Cahoot is the better long-term investment for sellers looking to streamline operations across multiple platforms.
If you’re running a high-volume ecommerce business that ships across multiple sales channels, handles inventory in multiple locations, or simply wants to reduce costs and errors at scale, Cahoot is the clear winner.
Don’t settle for free if it slows your business down.
Choose smarter. Explore how Cahoot can simplify your shipping and scale with your brand.
Frequently Asked Questions
Is Veeqo really free, and what’s the catch?
Yes, Veeqo is technically free, but many sellers report that key features like bulk shipping, inventory management, and reporting are limited. You may still need your own carrier accounts, and support can be slow.
How does Cahoot’s shipping software help reduce shipping costs?
Cahoot gives sellers access to discounted rates across major carriers like UPS, FedEx, and USPS, with no Veeqo credits or software bugs required. Plus, bulk shipping tools and data-driven insights help optimize your entire shipping process.
Can I use Cahoot if I sell on Amazon and other ecommerce channels?
Absolutely. Cahoot supports multiple sales channels, including Amazon, Walmart, eBay, and Shopify, while keeping inventory levels synced across all platforms. Unlike Veeqo’s integration, Cahoot’s system is fast, clean, and flexible.
What makes Cahoot better for inventory management than Veeqo?
Cahoot simplifies multi-channel inventory with real-time stock tracking, automated syncing, and alerts to prevent overselling. Veeqo users often struggle with managing inventory across platforms due to sync lags and poor data visibility.
Why do sellers leave Veeqo for Cahoot?
Many sellers switch when they realize Veeqo’s free model comes with trade-offs: limited support, Amazon ownership, clunky UI, and frustrating data export issues. Cahoot offers a full-featured, seller-first solution that saves time and drives smarter decisions.
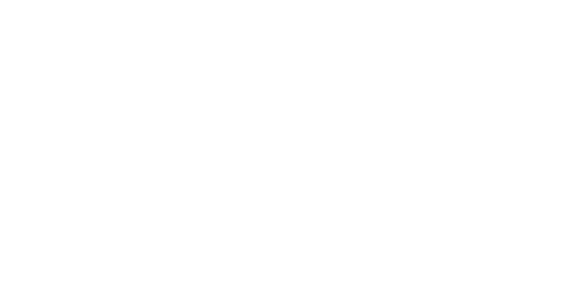
Turn Returns Into New Revenue
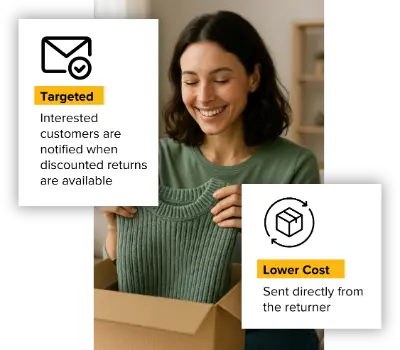
Peer-to-Peer Returns Platform: How It Benefits Emerging DTC Brands
Returns are the terrible, horrible, no good, very bad part of running an ecommerce business. Not just for shoppers (waiting around for a refund) but for emerging ecommerce brands, especially DTC operations. Every return cuts into profit, eats up time, and piles up inventory no one wants to touch. But here’s the twist: what if returns didn’t go back to the warehouse at all? What if they went directly to a new buyer instead? That’s the magic behind the peer-to-peer returns platform. This model introduces key advantages for DTC brands, such as reducing costs, minimizing waste, and improving customer satisfaction.
Cahoot, known for shaking up ecommerce logistics, is leading the charge with this innovative approach in the peer-to-peer returns space. And no, it’s not a borrowing scheme like peer-to-peer lending or a financial product like personal loans. But it does borrow some DNA from those systems, distributed networks, smart matching, and skipping the middleman. Online platforms in the peer-to-peer space facilitate these direct connections, much like how they connect borrowers and lenders in financial contexts, streamlining the process for all parties involved. Think of it as the social lending of ecommerce returns, where the system connects returners directly with new buyers, just as peer-to-peer platforms connect borrowers directly with lenders.
The Real Pain of Traditional Returns
Traditional returns work like this: a customer changes their mind, prints a label, ships the item back to you, and then you have to receive, inspect, restock, maybe repackage, and eventually resell it, often at a steep discount. Add in return shipping costs, warehouse labor, customer service tickets, and even potential late fees for delayed processing, and it’s a recipe for negative ROI.
For a small ecommerce business or a founder running lean, this isn’t sustainable. Shipping every return back to your warehouse is like using a bank account with constant fees and zero interest. It drains your cash flow. You could compare it to funding loans with higher risk and low return, much like the challenges faced with traditional loans when penalties and late fees add up. Frankly, it’s a bad deal.
Enter Peer-to-Peer Returns
Instead of sending the returned item to your fulfillment center, Cahoot’s peer-to-peer returns platform lets the original customer ship it directly to a new buyer. Here’s how it plays out:
1. A customer initiates a return.
2. The platform asks them to upload photos, confirm the condition, and hold the item for a few days.
3. AI kicks in, verifying the item’s resale quality, analyzing the returner’s history, and scanning for fraud (risk management). The platform’s technology enables streamlined processes, making the entire experience faster and more user-friendly.
4. Meanwhile, the item is automatically relisted on your store as open-box in real-time, discounted slightly, but still your branded product. The relisting and resale process is transparent and clear, much like how peer-to-peer lending platforms provide comparable loan terms, so both buyers and sellers know exactly what to expect.
5. When a new customer buys it, the returner gets a label to ship it out directly.
6. They’re refunded once tracking confirms it’s on the way or received. In terms of risk management, the risk of a single failed return transaction can be compared to a single default event in lending, highlighting the importance of robust verification and diversification strategies.
Now, instead of a refund eating your margins, you’re reselling the item at 85–95% of retail, skipping warehouse handling and double shipping. It’s fast. It’s efficient. And yes, it saves money.
Slash Your Fulfillment Costs by Up to 30%
Cut shipping expenses by 30% and boost profit with Cahoot's AI-optimized fulfillment services and modern tech —no overheads and no humans required!
I'm Interested in Saving Time and MoneyWhy This Works (Especially for Small Businesses)
This isn’t just a fun gimmick. Cahoot’s peer model addresses real ecommerce challenges:
- Shipping Costs: You skip the return leg to the warehouse.
- Inventory Management: The item never clogs up your system.
- Speed: New customers get the item faster. Returners get refunded sooner.
- Customer Satisfaction: Everyone feels good helping the planet and their wallet.
For small businesses, this model is similar to how small business loans and business loans provide alternative financing options to cover major expenses, supporting growth and development when traditional funding is limited.
It’s like a micro version of peer lending. Instead of funding loans with capital, you’re moving product through customer participation. Instead of worrying about borrower defaults, you’re focused on buyer satisfaction and ensuring compliance through verified transactions. The platform also helps brands achieve their financial goals by offering accessible and flexible solutions. Other benefits of the peer-to-peer returns model include improved business insights, better payment terms, and fostering a supportive community for both buyers and sellers.
The Financial Angle
Okay, let’s talk money. The traditional return process? It’s basically like investing in traditional savings accounts, low return, high friction. With peer-to-peer returns, you’re now in the world of alternative investments. You’re getting more value, faster turnover, and lower risk.
Just as peer-to-peer (P2P lending) platforms allow individual and institutional investors to invest in loans, with returns shaped by interest rates and regular interest payments, our model lets you realize value more efficiently. On lending platforms and lending sites, loan offers are determined by factors like minimum credit score, good credit, and the borrower’s profile, much like how our platform assesses transaction eligibility and risk.
Your effective recovery rate improves. That espresso machine that used to cost you $50 to restock and repackage? Now it’s resold in 72 hours at 90% retail with no warehouse touch. That’s the kind of turnaround most lending sites or lending platforms would kill for.
Built-In Risk Management
Cahoot doesn’t wing it. Our P2P returns platform is built with risk tolerance settings, fraud detection layers, and condition verification, all using AI. That means you’re not just trusting your customers blindly. These tools empower brands to make informed decisions about approving returns and managing risk.
It’s like when institutional investors assess borrower defaults, they don’t rely on vibes. They crunch data, assess credit risk, and build safeguards. Cahoot’s doing the same for your returns: historical data, photo analysis, shipping trends, and user history all factor into who gets approved for peer-to-peer returns.
Customer Experience
Customers like this model. It’s interactive. It feels more personal. They get to feel like part of a sustainability loop. It’s like when borrowers connect with individual lenders on lending platforms, there’s emotional value. A product gets rehomed instead of returned to some faceless warehouse.
Returners are rewarded with small credits or perks for participating. Buyers get a deal. You recover more revenue. And the planet breathes a little easier. That’s what we call attractive returns.
Wrapping It Up
Peer-to-peer returns aren’t just a clever workaround; they’re a full-on rethinking of ecommerce reverse logistics. For small business owners, they offer a practical way to save money, improve customer satisfaction, and align with sustainability goals. For larger brands, they unlock serious cost savings and scalability.
So, whether you’re selling sneakers, smart home gear, or skincare, if returns are eating your margins, it might be time to make a move.
Because unlike traditional financial institutions, this isn’t built on bureaucracy. It’s built on agility, innovation, and a willingness to rethink the rules. Sound familiar?
That’s ecommerce done smarter.
Frequently Asked Questions
What is a peer-to-peer returns platform, and how does it work?
A peer-to-peer returns platform connects the original buyer of a product with a new customer who wants to purchase it, avoiding the need to ship the item back to the brand’s warehouse. Instead of returning it to a traditional logistics hub, the returner ships the item directly to the next buyer. This innovative approach reduces return costs, speeds up resale, and supports sustainability goals for small businesses.
How is a peer-to-peer returns model different from traditional returns?
Traditional returns involve sending the product back to a brand or warehouse, where it’s inspected, restocked, and resold. A peer-to-peer system skips that step. The original buyer holds the item temporarily while the platform finds a new buyer. Once sold, the item ships directly to the new customer, eliminating an entire shipping leg and creating a more efficient, cost-saving process similar to how peer-to-peer lending eliminates middlemen in finance.
Are peer-to-peer returns safe for ecommerce businesses and customers?
Yes. Platforms like Cahoot use advanced fraud detection, data analytics, and AI verification to ensure the returned item matches quality standards before resale. Buyers can review photos, condition grades, and return policies. Just like in peer lending, where borrower defaults are managed through credit checks and risk scoring, P2P returns include safeguards to protect both original and new customers.
What types of ecommerce brands benefit most from peer-to-peer returns?
Virtually any ecommerce brand can benefit from peer-to-peer returns as long as the products aren’t perishable, dangerous (hazmat), or otherwise require a tighter level of control (contamination concerns). From emerging DTC brands and small businesses to large enterprises, companies offering fast-moving consumer goods see the biggest gains. Peer-to-peer returns help reduce operating costs, improve cash flow, and increase customer satisfaction, especially for businesses without access to traditional loans, large warehouses, or institutional investor backing.
How can I start using a peer-to-peer returns platform?
To get started, ecommerce sellers can partner with a platform like Cahoot that offers peer-to-peer returns as part of its fulfillment solution. The platform handles the tech, including photo-based grading, shipping logistics, and fraud prevention. It’s as simple as integrating the system, setting product eligibility rules, and letting the platform connect returns with new buyers, streamlining processes, and unlocking attractive returns on previously lost sales.
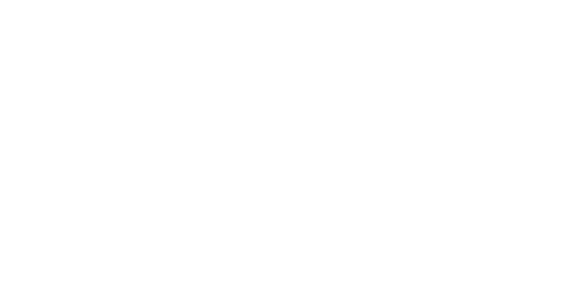
Turn Returns Into New Revenue
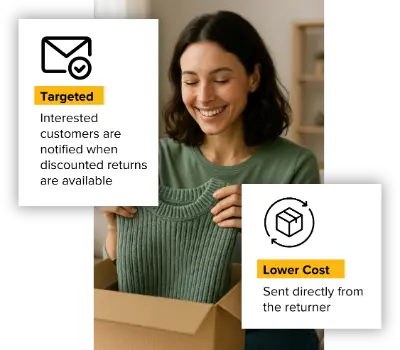
How AI-Powered Cahoot Returns Management Reduces Ecommerce Fraud
In this article
9 minutes
- The Real Cost of Returns Fraud
- How AI Detects Fraud in the Returns Process
- How Cahoot Uses AI to Catch Return Fraud Before It Hits Your Warehouse
- How AI Preserves Customer Trust
- Behind the Scenes: What AI Actually Looks At
- The Business Benefits
- Final Thoughts: AI Is the Future of Fraud Prevention
- Frequently Asked Questions
Fraudulent returns and refund abuse are eating into ecommerce profits like termites in a timber shack. We’re not just talking about a few bad actors. This is a systemic issue. Every time someone pulls a fast one, returning a used dress, faking a receipt, or claiming a package never arrived, ecommerce businesses bleed money. But here’s the good news: AI is finally catching up.
Businesses that implement AI-powered fraud detection tools gain a competitive advantage in the ecommerce space, reducing losses and improving operational efficiency.
This article explores how AI-powered returns management is giving merchants the upper hand, using machine learning and advanced fraud detection tools to sniff out shady behavior while keeping the experience smooth for legitimate customers. The tech is here, it’s learning fast, and it’s reshaping how we handle ecommerce returns.
The Real Cost of Returns Fraud
Returns fraud isn’t just annoying, it’s financially devastating. Think about:
- Wardrobing: Wear once, return as “new”.
- Switch fraud: Return a knockoff and keep the real thing.
- Empty box scams: Return a box with no item inside, claim it’s there.
- Refund fraud: Claim the item never arrived, even when it did.
Customers exploit return policies by making false claims about product defects or delivery issues, manipulating the system for personal gain. Fraudulent return activities also include stolen merchandise returns and targeting high-value items such as luxury goods.
All of these fall under fraudulent returns and refund fraud, and they’re on the rise. According to the National Retail Federation, ecommerce losses from return abuse now top tens of billions of dollars annually.
AI analyzes return data and return patterns to identify patterns and fraud patterns in return transactions, helping businesses detect and prevent evolving forms of return fraud.
The old methods, manual checks, strict return policies, and restocking fees, aren’t cutting it anymore. They hurt genuine customers and barely scratch the surface of sophisticated scams. That’s where AI fraud detection for ecommerce returns steps in.
How AI Detects Fraud in the Returns Process
AI-powered returns management combines machine learning algorithms, transaction data, returns data, and customer behavior to spot bad actors before they strike. AI-powered systems are designed to prevent fraud throughout the returns process. Here’s how:
1. Photo Verification & Image Recognition
AI can evaluate customer-submitted images of returned items to:
- Detect box fraud or item switching.
- Compare the product’s appearance to a verified new version.
- Identify wear, missing parts, or damage that contradicts the return reason.
This allows brands to detect fraudulent activity before it’s even shipped back.
2. Pattern & Anomaly Detection
Machine learning excels at spotting unusual patterns in behavior:
- Return frequency: Has the customer returned too many high-value items?
- Geolocation: Is the return request coming from a region known for return scams?
- Purchase timing: Did they buy during a sale and return right after peak season?
These patterns raise fraud risks and trigger review or denial workflows.
3. Cross-Platform and Channel Monitoring
AI systems can check across multiple returns and ecommerce channels, identifying if a return was initiated:
- For the same item on multiple platforms.
- Using fake receipts.
- From a buyer who already claimed store credit somewhere else.
AI can also monitor for account takeover attempts by detecting unusual account activities, such as frequent address changes, excessive returns, or high-value purchases. When suspicious account activity is detected, AI can recommend enabling multi-factor authentication to add an extra layer of security and prevent unauthorized access.
This multi-touch intelligence is a game-changer for fraud prevention goals.
4. NLP for Reason Analysis
Natural language processing (NLP) can analyze written return reasons and flag:
- Repeated use of vague claims like “defective”.
- Scripted language that suggests fraud rings.
It’s subtle, but over time, it sharpens fraud detection and helps businesses adapt.
5. Smart Risk Scoring
With returns management systems like Cahoot, each return is assigned a fraud risk score based on:
- Customer history
- Returns data
- Known red flags like frequent returns, high-value items, high-risk transactions, or mismatched shipping info
High-risk returns may trigger:
- Photo verification
- Manual review
- Limited refunds (e.g., store credit only)
How Cahoot Uses AI to Catch Return Fraud Before It Hits Your Warehouse
Here’s the short version: Cahoot’s AI-powered returns system sniffs out sketchy returns before they even hit your dock. No detective hats or magnifying glasses required. It’s proactive fraud prevention baked right into the returns process, built for ecommerce teams who don’t have time (or money) to waste on refund fraud and box scams.
Here’s how it plays out in real life: a customer clicks “return,” and instead of handing them a prepaid label like candy at a parade, Cahoot asks for photos. Item, packaging, maybe even the serial number. That’s when the AI kicks in, checking everything against the original order. Does the item match what was sold? Is the box suspiciously light? Are they trying to return a broken knockoff instead of the actual product? The system flags anything that smells off. No human has to squint at a blurry JPEG; AI’s doing the heavy lifting.
And if things look really fishy? Cahoot assigns a fraud risk score based on the customer’s history, return frequency, location, and transaction data. Say this person’s been sending back a lot of high-value items or triggering patterns tied to refund fraud, Cahoot might put the brakes on the refund, sending it to manual review or straight-up denying it. It’s like having a savvy fraud analyst on call, 24/7, who doesn’t need coffee breaks.
But that’s not all, it gets sharper with every return. The system learns what fraud looks like. Maybe it flags addresses linked to repeat offenders. Maybe it notices “this person always returns luxury goods two days before the return window closes.” The more it sees, the smarter it gets. Over time, it recommends policy tweaks that actually make sense, like tightening windows for excessive returns or requiring restocking fees on high-risk items.
Cahoot also checks serial numbers in real time. That means box fraud, where someone swaps the product and sends back a decoy, gets stopped cold. If the serial number doesn’t match what was sold? Game over. No refund. No restock. Just one more fake return that never made it through the door.
All of this happens quietly in the background, streamlining the returns process for good customers while catching the bad ones red-handed. That’s the beauty of machine learning in ecommerce returns: it doesn’t just react, it predicts. And when refund fraud can bleed your margins dry faster than a flash sale, that kind of protection isn’t just nice to have, it’s essential.
Cahoot’s AI isn’t trying to micromanage your returns team; it’s giving them superpowers. So your operations run leaner, your legit customers stay happy, and your profits stay where they belong. In your pocket.
How AI Preserves Customer Trust
One of the trickiest parts of returns fraud is not alienating loyal customers. Efficient returns processes powered by AI improve customer satisfaction by reducing friction and delays. A good AI doesn’t just block fraud, it enables a positive customer experience by:
- Fast-tracking legitimate customers
- Preventing false positives through layered detection
- Using customer verification sparingly and intelligently
In short, it finds the right balance between fraud prevention and a frictionless returns process.
Behind the Scenes: What AI Actually Looks At
This isn’t black magic, it’s smart automation trained on mountains of data:
- Historical data: Past behaviors of repeat offenders and loyal shoppers
- Data points: Shipping speed, order value, return time frame
- Customer data: Addresses, accounts, payment histories
- Delivery tracking: GPS drops vs. “item not received” claims
Together, these inputs help detect fraud across a spectrum, from empty box fraud to money laundering via returns.
The Business Benefits
When ecommerce companies implement AI-powered returns management, they see results fast. These benefits contribute to the long-term success of ecommerce businesses:
✔ Reduced Operational Costs
- Less need for manual review
- Faster returns management process
✔ Improved Customer Loyalty
- Quicker refunds for genuine customers
- Confidence that return policies are fair
✔ Higher Margins
- Fewer fraudulent returns and chargebacks
- More high-value items are resold instead of being written off
✔ Smarter Policy Decisions
- AI insights guide better rules
- Target return abuse without punishing everyone
It’s a full-circle win for ecommerce businesses who want to scale securely.
Final Thoughts: AI Is the Future of Fraud Prevention
Return fraud is constantly evolving. So are the tools to fight it. By leveraging AI and machine learning in the returns management space, sellers are turning what used to be a liability into a competitive edge.
With platforms like Cahoot, advanced technology no longer belongs only to the big guys. Even mid-size online stores can now fight receipt fraud, friendly fraud, and return scams with precision.
So next time someone tries to game the system with a personal gain hustle, just remember: AI sees all. And it doesn’t blink.
Frequently Asked Questions
How does AI detect fraudulent returns in ecommerce?
AI fraud detection for ecommerce returns works by analyzing returns data, customer behavior, and product images to identify suspicious patterns. It can flag issues like empty box fraud, receipt fraud, or mismatched serial numbers by comparing return requests against historical transaction data and trained machine learning algorithms.
What is the difference between return abuse and friendly fraud?
Return abuse often involves intentional schemes like wardrobing or box switching for personal gain, while friendly fraud includes tactics like claiming an item was never received to get a refund. Both forms of fraudulent activity are increasing in ecommerce returns, and AI-powered systems help detect these behaviors quickly.
Can AI-powered returns management improve customer satisfaction?
Yes. By separating legitimate customers from bad actors, AI-powered returns management allows genuine customers to experience faster processing, easier refunds, and less hassle, while fraudsters face more scrutiny. This helps maintain customer loyalty, customer trust, and a positive customer experience.
What types of ecommerce return fraud does AI help prevent?
AI helps identify and prevent a range of fraud types, including stolen merchandise returns, false claims, empty box fraud, refund fraud, and return scams. It uses data points like return frequency, image analysis, and customer history to flag high-risk transactions for further review.
Why is AI better than traditional fraud prevention methods?
Unlike manual reviews or blanket return policies that can frustrate loyal customers, AI fraud detection tools use advanced technology to spot fraud patterns in real-time. This results in lower operational costs, stronger fraud defenses, and better long-term success for ecommerce businesses.
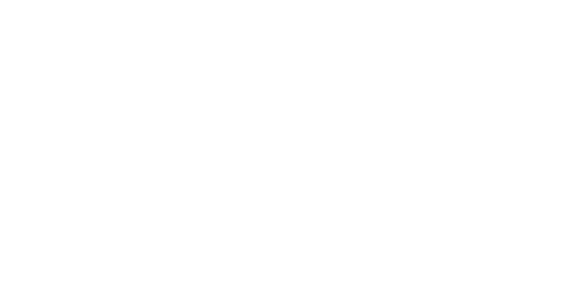
Turn Returns Into New Revenue
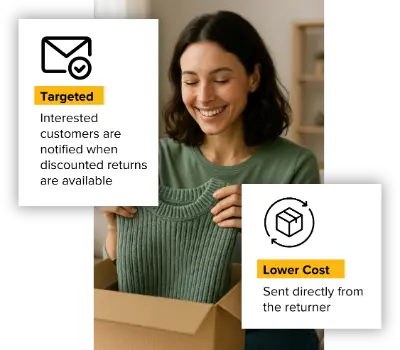
Strategies to Mitigate FedEx and UPS Surcharges 2025
In this article
9 minutes
- Why Are These Surcharges Getting Worse?
- What This Means for Your Ecommerce Operation
- 1. Know Your Surcharge Triggers
- 2. Reroute Using Distributed Fulfillment
- 3. Leverage Regional Carriers and USPS
- 4. Negotiate Like a Pro
- 5. Bundle Smart and Reduce Dead Weight
- 6. Offer Incentives to Offset Costs
- 7. Monitor, Adjust, Repeat
- 8. Stay Compliant: Commercial Invoice Requirements
- Final Thoughts
- Frequently Asked Questions
Let’s not sugarcoat it. The 2025 UPS and FedEx surcharges are hitting hard, and if you run an ecommerce business, you’re likely already feeling it in your margins. These aren’t just petty rate hikes; we’re talking residential delivery fees, large package surcharges, and peak season multipliers that could straight-up wreck your bottom line if left unchecked. New surcharges and additional fees can quietly inflate costs for ecommerce businesses if not monitored closely.
So what do we do? Panic? Raise prices? Light a candle? Nah. Let’s talk smart ecommerce shipping strategy. This article will help you identify and address these additional fees before they quietly eat into your profits.
Why Are These Surcharges Getting Worse?
Simple: higher costs for carriers, inflation, delivery network strain, and the never-ending Amazon arms race. Carriers know ecommerce businesses rely on them, and they’re capitalizing on that reliance with complex, hard-to-negotiate fees. To increase revenue, carriers are introducing new surcharges and modifying their pricing structure, resulting in additional revenue streams that shippers must monitor closely.
It used to be seasonal. Now it’s structural. UPS recently added a higher “Additional Handling” fee for packages over 30 pounds, and FedEx followed suit with new zone-based surcharges on bulky items. These changes are part of the evolving UPS surcharges landscape, reflecting how carriers are using new fees and pricing structure adjustments to drive revenue. If your business ships large packages (think fitness gear, small furniture, or bundled orders), you’re in the crosshairs.
What This Means for Your Ecommerce Operation
These aren’t line items you can just absorb. Surcharges and fees affect not just shipping costs but also other aspects of your business, including a new 2 percent payment processing fee on most charges. If you’re not actively working to reduce shipping costs with UPS and FedEx, you’re leaving money on the table, or worse, eating it. That “free shipping” promise starts to feel like a bad joke.
Changes in shipping rates and surcharges can significantly impact shippers’ bottom lines. This is where shipping strategy becomes a profit lever.
1. Know Your Surcharge Triggers
First up: audit your shipments. Where are the fees coming from?
- Oversize or large package fees? (Services affected: typically ground and express shipments)
- Residential delivery? (Services affected: home delivery and residential ground services)
- Peak delivery windows? (Services affected: all expedited and time-definite services)
- ZIP codes with higher fees (“extended area surcharge”)? (Services affected: rural and remote area deliveries; charges subject: extended area surcharges)
Understanding which charges are subject to surcharges for each package shipped is crucial for controlling shipping costs and optimizing your logistics strategy.
Use this data to model scenarios: “What happens if I split shipments differently? Consolidate? Change carriers regionally?”
2. Reroute Using Distributed Fulfillment
If you’re shipping coast-to-coast from a single warehouse, you’re stacking up zone charges. A 4 lb box from NYC to Oregon isn’t the same cost as one going to Jersey.
Using distributed fulfillment cuts zone distance, enables faster delivery, and reduces per-package surcharge exposure, including those related to domestic ground shipping services. This is especially important for large or heavy ecommerce products.
Additionally, consolidating shipments can further minimize surcharge costs.
3. Leverage Regional Carriers and USPS
Don’t let UPS and FedEx think they’re the only game in town. Regional carriers like OnTrac and LSO are expanding coverage and love ecommerce volume. For lighter shipments, USPS remains competitive and immune to many surcharge layers. However, keep in mind that services like UPS Ground Saver® and various air services, including UPS Next Day Air, UPS 2nd Day Air, and international air options, are also subject to changing fuel surcharges, which can impact your shipping costs.
Use carrier rate shopping logic to auto-select the most affordable carrier based on destination, weight, and dimensions, and consider how surcharges on UPS Ground Saver and air services may affect your total rates.
4. Negotiate Like a Pro
Yes, you can negotiate UPS and FedEx rates, but you need leverage. Demonstrating high shipping volume and effectively managing frequent shipments can provide significant bargaining power. Show them your volume growth, historical performance, and willingness to shift volume elsewhere. Push for:
- Waived or reduced surcharges
- Custom DIM divisor
- Discounts for specific ZIPs or package types
- Better terms on traditional shipping rates and all ancillary fees, not just base rates
And don’t just do this once a year. Re-negotiate quarterly if needed.
5. Bundle Smart and Reduce Dead Weight
Product bundling sounds simple until you realize you’re accidentally triggering dimensional weight charges or bumping into a surcharge tier. Optimizing packaging can provide value-added benefits and reduce the risk of incurring extra surcharges.
Use cartonization software or fulfillment logic to optimize what goes in each box. Small tweaks to packaging design or SKU mix can save you thousands.
6. Offer Incentives to Offset Costs
Let your customers help. Offer:
- Store pickup or local delivery discounts
- Extended delivery timelines for lower-cost options
- Free shipping thresholds to encourage higher-margin AOVs
You’re not passing on fees, you’re framing value.
7. Monitor, Adjust, Repeat
Surcharges change quarterly, and as mentioned, fuel surcharges are especially important to monitor as they can significantly bump your shipping costs. Fluctuating fuel prices directly impact how carriers adjust fuel surcharges, so it’s essential to track these changes and adjust your strategies accordingly. Don’t wait for the damage to show up in your P&L. Set up automated reporting by carrier, SKU, zone, and surcharge type. Watch trends.
A client of ours shipping workout gear will trim \$40 K from their shipping budget by simply redesigning two SKUs to avoid “additional handling” fees. Total cost: \$3 K in packaging R&D.
Recent changes include more frequent updates to fuel surcharges based on weekly fuel price indices, and new surcharge structures that can significantly bump costs if not closely monitored. The key takeaway: Stay proactive by tracking all surcharges, especially those affected by fluctuating fuel prices, and be ready to adjust your shipping strategies to minimize the impact on your bottom line.
8. Stay Compliant: Commercial Invoice Requirements
If you think surcharges only hit you at the shipping label, think again. Earlier this year, UPS rolled out a new “Paper Commercial Invoice Service Surcharge,” meaning every time you send a shipment with a paper commercial invoice, you’ll get dinged with an extra fee. For businesses still relying on traditional invoicing methods, this is one more way shipping costs can quietly inflate.
A commercial invoice isn’t just paperwork; it’s a required document for international shipments, detailing what’s in the box, its value, and who’s sending and receiving it. Get it wrong, and you risk delays, compliance headaches, or even more fees. Get it right, and you keep your shipments moving and your costs in check.
To avoid this new surcharge, start paying closer attention to your invoicing processes. Switching to digital form, electronic invoicing (e-invoices) not only helps you dodge the UPS paper invoice fee but also streamlines your shipping workflow and reduces manual errors. Make sure your shipping software or logistics provider supports digital commercial invoice generation and submission.
Bottom line: staying compliant with commercial invoice requirements isn’t just about avoiding penalties, it’s about keeping your shipping costs under control and your business running smoothly. Don’t let outdated invoicing practices add unnecessary fees to every shipment. Embrace digital, stay ahead of the surcharges, and keep your logistics costs lean.
Final Thoughts
The 2025 UPS and FedEx surcharge landscape isn’t going to let up. But ecommerce brands that treat shipping like a strategic function, not a static cost, will thrive.
To succeed, adopt a holistic approach to managing logistics costs across your entire supply chain. This means not only focusing on shipping rates, but also understanding how payment processes, payment habits, and payment fees impact your bottom line. Regularly review your payments strategy to optimize for efficiency and maintain healthy cash flow.
Be aware that late payment fees, processing fees, and payment fees on most invoice charges can quickly add up, disrupting cash flow and increasing overall expenses. Late payers face a steep 9.9 percent late fee, and prior late fees will be incorporated into your past-due balance, compounding the cost of overdue accounts. Tracking each transaction and understanding the fee per payment method, whether ACH payments, wire transfers, or paper invoices, is essential for cost control.
Traditional payment methods now often incur additional charges, so consider switching to ACH payments, which are typically fee-free and help streamline payment processes. Avoid extra costs by moving away from paper invoices and printed invoice copies, as these now come with a \$5 fee per invoice. Digital invoicing solutions can help you save money and improve efficiency.
Always check the effective date of new surcharges and payment policy changes to ensure compliance and avoid unexpected costs. For expert guidance on navigating these changes and optimizing your logistics strategy, consult with an expert.
Audit. Distribute. Negotiate. Automate. Adjust.
It’s not about fighting surcharges with brute force. It’s about outsmarting them.
So take a deep breath, pull up your shipping data, and start cutting where it counts. The savings are there. You just have to dig.
Frequently Asked Questions
What are the new UPS and FedEx surcharges for 2025?
UPS and FedEx have introduced increased surcharges in 2025 for large packages, residential deliveries, and fuel costs, significantly impacting ecommerce shipping expenses.
How can ecommerce brands reduce the impact of surcharges on large packages?
Brands can redesign packaging to meet dimensional thresholds, negotiate cubic pricing, or split shipments when appropriate to avoid oversized surcharges.
Can smaller ecommerce stores negotiate lower UPS and FedEx rates?
Yes, especially by leveraging third-party fulfillment networks or 3PLs that aggregate volume across multiple sellers, giving them stronger negotiating power.
Is it worth switching carriers due to the 2025 surcharge changes?
That depends on your shipping profile. Some regional carriers or hybrid services may offer better rates and fewer surcharges for specific zones or package types.
What role does shipping software play in managing surcharge costs?
Shipping software can help reroute orders, compare carrier rates in real-time, and optimize label selection to minimize surcharges and boost cost efficiency.
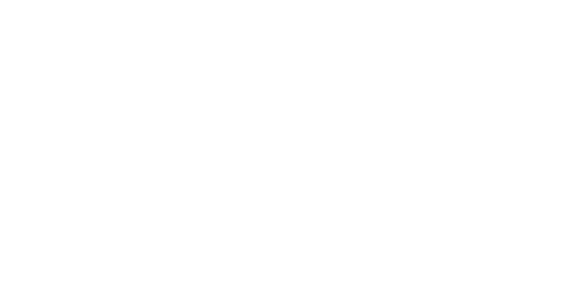
Turn Returns Into New Revenue
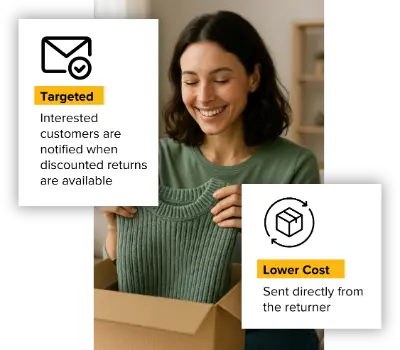
Reduce the Carbon Footprint of Ecommerce Returns Without Greenwashing
In this article
12 minutes
- Returns: The Hidden Carbon Emissions Sustainability Sinkhole
- The Problem with Offsets
- The Role of Fast Fashion in Ecommerce Returns
- What to Do Instead: Real Strategies for Sustainable Returns
- The Importance of Transparency and Accountability
- Reducing Environmental Impact through Education
- The Bigger Picture: Returns as a Circular Opportunity
- TL;DR: Stop Offsetting, Start Optimizing
- Frequently Asked Questions
Let’s get one thing out of the way: buying carbon offsets isn’t a silver bullet. Sure, they might make a brand feel better. Throw some money at a reforestation project, slap a “carbon neutral” badge on the website, and call it a day. But customers? They’re not fooled anymore. The modern ecommerce shopper is savvier, more eco-aware, and has a nose for greenwashing from a mile away. With the rise of ecommerce, online returns have become increasingly common, adding new layers of complexity to sustainability efforts.
So, what can a brand actually do to make ecommerce returns more sustainable without hiding behind offsets and hope? Returns are the ecommerce world’s dirty secret. Returns significantly affect the environment by increasing emissions, packaging waste, and resource use due to the logistics involved in processing returned items.
Let’s talk about it.
Returns: The Hidden Carbon Emissions Sustainability Sinkhole
Returns are the ecommerce world’s dirty secret. That stylish jacket that gets sent back because the fit’s off? It’s not always going back on the shelf. Sometimes it’s rerouted halfway across the country, sometimes it’s trashed. Literally. Return parcels often travel long distances, sometimes internationally, adding significantly to carbon emissions.
According to industry estimates, ecommerce returns generate over 15 million metric tons of carbon emissions per year. Return shipping is a major contributor to these emissions, as the logistics of moving products back through the supply chain are often more complex than the original shipment. That’s not counting the packaging waste, the reverse logistics, or the markdown losses that fuel overproduction. In fact, the emissions from returns can be up to 30% higher than those from the initial delivery, and the return process can take up to three times longer than the initial delivery time, further increasing environmental strain.
And it’s only getting worse.
Returns are expected to increase in volume as online shopping keeps growing. Which means if a brand is serious about sustainability, this is the battleground. This is where the carbon battle is won or lost. Optimizing the return process is essential to reducing environmental impact and achieving true sustainability.
The Problem with Offsets
First, what are carbon offsets? Carbon offsets are a way to compensate for greenhouse gas emissions by funding projects that reduce or remove those emissions elsewhere. They represent a financial instrument, often in the form of carbon credits, that can be bought and sold to offset a company’s or individual’s carbon footprint. Essentially, you pay someone else to reduce emissions so you can balance out your own impact. Some refer to this practice as “greenwashing,” that is, misleading marketing that creates a positive public image as it relates to sustainability efforts, when in reality, companies are simply throwing money at the problem.
Offsetting carbon emissions has become the default sustainability strategy for many ecommerce brands. But let’s call it what it often is: a shortcut. It’s easier to buy carbon credits than to rethink logistics. But it’s also increasingly under scrutiny.
Customers and regulators alike are asking hard questions:
- Are these offset projects even real?
- Are they additional (i.e., would they have happened anyway)?
- Are they permanent?
- Are they actually reducing emissions or just moving guilt around?
If the answer to any of those is fuzzy, that shiny “carbon neutral returns” badge starts to look more like PR theater than real progress.
The Role of Fast Fashion in Ecommerce Returns
Fast fashion is a major driver behind the mountain of ecommerce returns and the environmental impact that comes with it. The fashion industry records some of the highest return rates, thanks to a business model built on rapid trends, low prices, and disposable products. This cycle encourages customers to buy more, try more, and return more, often with little thought to the consequences.
The result? A huge environmental impact. Every returned fast fashion item means more transportation, more packaging waste, and substantially more emissions. Many of these items are made from low-quality materials, making them harder to resell or recycle and more likely to end up in landfills.
Online retailers in the fashion industry can help break this cycle by adopting sustainable return processes. This means making it easier for customers to get sizing and fit right the first time, offering detailed product information, and encouraging customers to think twice before making impulse purchases. By promoting mindful shopping and streamlining return processes, online retailers can reduce unnecessary returns and their associated emissions, helping to create a more sustainable future for fashion.
What to Do Instead: Real Strategies for Sustainable Returns
Let’s dig into actual solutions that reduce the carbon footprint of ecommerce returns without playing the offset game.
1. Don’t Ship What Doesn’t Need to Be Returned
Before we talk transportation, let’s talk logic. Some returns just… shouldn’t happen. For instance:
- Low-cost items where shipping back costs more than the refund.
- Used or damaged items are better suited for resale, donation, or recycling.
Free returns policies often encourage customers to return more products, even when it’s unnecessary. As a result, customers return a significant percentage of online purchases, especially in categories like clothing, leading to high volumes of returns. This means customers sending back items unnecessarily, which increases emissions, packaging waste, and environmental impact.
Amazon, Target, and others are experimenting with “keep it” policies. It’s not charity, it’s math. And it slashes emissions.
Pro tip: Offer refunds or store credit for certain items without requiring them to be shipped back. Flag these automatically by value or category.
2. Make Online Returns Local
Centralized return centers? Good for control. Bad for emissions. Every mile adds CO₂. When return parcels travel long distances to centralized locations, they significantly increase carbon emissions. Return shipping over extended routes not only raises costs but also has a substantial environmental impact.
Instead, build a distributed returns network using local micro-fulfillment centers, third-party dropoff points (like Happy Returns), or even store partners. Let returns travel shorter distances and restock closer to the next buyer, optimizing the returns process for local returns.
Pro tip: If you run a Shopify store, check out apps that integrate dropoff points or enable peer-to-peer returns.
3. Sell Returns Before They Ship
This one’s juicy. Some startups (yes, Cahoot is in this space) are enabling returns rerouted directly to the next buyer.
Say a customer in Dallas returns a pair of shoes. Instead of shipping them to a return hub in Ohio, list them instantly on your site as “open box,” and fulfill the next order right out of the first customer’s hands. The resale value of these products is a key economic consideration, as it may not always cover the expenses involved in the returns process. But in general, fewer miles, less waste, happier planet.
Pro tip: Market “returned but good as new” inventory as a value-conscious, sustainable choice for the next buyer.
4. Fix Fit, Friction, and Frustration
A huge chunk of returns aren’t defects; they’re disconnects.
- “This doesn’t fit like I thought it would.”
- “The color’s off.”
- “I didn’t realize it needed batteries.”
These issues often arise when customer expectations are not clearly set or managed. Meeting or exceeding customer expectations through clear product information and communication is crucial to reducing returns.
Every return like that is a failure of expectation-setting. Use smarter sizing guides, AR try-on tools, richer product pages, and yes, better post-purchase communication to prevent avoidable returns altogether.
Pro tip: Track return reasons obsessively. Fix the upstream problem.
5. Consolidate Reverse Logistics
Every one-off return is a sustainability nightmare. Smart brands offer:
- Scheduled return pickups
- Bundled return shipments
- QR-code dropoffs that batch items into optimized routes
Optimizing returns processes is crucial for sustainability; streamlining each step reduces waste and environmental impact.
Instead of one label, one box, one truck, turn returns into networked events. Fewer trips, fuller trucks, smaller footprint.
Pro tip: Work with 3PLs or carriers that offer consolidated reverse logistics as part of their service model.
6. Rethink Packaging and Waste
Packaging is often the first thing customers see, and the first thing they throw away. Rethinking packaging and waste is a powerful way to shrink the carbon footprint of ecommerce returns. Start by swapping out traditional materials for sustainable packaging options: think biodegradable mailers, recyclable boxes, and paper-based alternatives to plastic bubble wrap.
But don’t stop there. Encourage customers to reuse packaging for their returns, or even for other purposes at home. A simple “reuse and recycle” message in your return instructions can go a long way toward minimizing waste. Some brands even offer incentives for customers who return items in their original packaging.
By prioritizing sustainable packaging and minimizing waste, online retailers can cut environmental costs and help build a more sustainable future, one return at a time.
7. Leverage Technology for Smarter Returns
Technology is a game-changer when it comes to optimizing return processes and reducing environmental impact. Virtual try-on technology lets customers see how clothes or accessories will look and fit before they buy, slashing the number of returns due to poor fit or style mismatches. This not only enhances customer satisfaction but also reduces the environmental footprint of online shopping.
AI-powered return management systems can further streamline return processes for online retailers. These tools can predict which items are most likely to be returned, automate approvals, and even suggest the most sustainable route for each return. The result? Faster, smarter returns that use fewer resources and generate less waste.
By embracing technology-driven solutions, online retailers can deliver a more positive customer experience while making meaningful progress toward sustainability.
The Importance of Transparency and Accountability
In the ecommerce industry, transparency and accountability are non-negotiable for reducing the environmental impact of returns. Customers want to know exactly how their returns are handled, where items go, how waste is minimized, and what steps are being taken to reduce emissions.
Online retailers should clearly communicate their return policies and processes, making it easy for customers to understand what happens after they send something back. This includes being upfront about efforts to minimize waste, use sustainable materials, and optimize return processes for lower emissions.
By holding themselves accountable and sharing their progress, online retailers can build trust, set themselves apart in a crowded market, and drive the entire industry toward more sustainable practices.
Reducing Environmental Impact through Education
Education is a powerful tool for reducing the environmental impact of ecommerce returns. Online retailers have a unique opportunity to inform customers about the environmental costs of returns and the benefits of making more sustainable choices.
This can be as simple as including information on product pages about the carbon footprint of returns, or as involved as partnering with environmental organizations to promote sustainable shopping habits. By raising awareness and encouraging customers to think before they buy or return, retailers can help shift behavior toward a more sustainable future.
Empowering customers with knowledge not only reduces waste and emissions but also strengthens brand loyalty and positions online retailers as leaders in building a more sustainable ecommerce industry.
The Bigger Picture: Returns as a Circular Opportunity
Sustainability isn’t just about less carbon. It’s about less waste, less overproduction, and more reuse. Using more sustainable materials in returned products can significantly reduce the environmental impact and support circularity.
Returned items don’t have to be liquidated, dumped, or buried in clearance tabs. With the right tech stack and reverse logistics flow, returns can fuel:
- Refurbished product lines
- Second-chance marketplaces
- Loyalty-building exchanges
- In-house recommerce
However, the process of handling returns often generates extra packaging materials, excess packaging, plastic packaging, plastic waste, and plastic packaging waste, all of which contribute to environmental impact and landfill accumulation. Returned synthetic products can emit plastic particles, further polluting the environment. Improper disposal of returned goods can even result in open-air dumping sites, as seen in some regions.
The scale of the problem is massive, with billions of pounds of returned products, specifically, 9.5 billion pounds, ending up in landfills each year. These practices contribute to global carbon emissions, greenhouse gas emissions, and CO2 emissions, highlighting the true environmental cost of ecommerce returns. Many synthetic materials in returned goods are produced using fossil fuels, compounding the emissions problem.
Certain categories, such as consumer electronics, present unique challenges due to hazardous materials and recycling difficulties. Compared to returns from online shopping, in-store purchases generally have lower return rates and generate less waste, making them more sustainable options. Thus, traditional shopping contributes less to packaging waste and emissions than ecommerce.
Online shopping returns and ecommerce returns, however, are associated with higher rates of returns, more packaging waste, and greater environmental cost. Online shopping leads to increased waste from online purchases, and the percentage of returns from online purchases varies widely by industry. The fashion industry recorded some of the highest return rates, further amplifying the issue.
The same emissions generated by reverse logistics, repackaging, and landfilling of returns are comparable to those produced by millions of cars. Paper waste is another significant byproduct of inefficient return processes.
Both consumers and retailers share responsibility for reducing the environmental impact of returns. Adopting sustainable practices can improve customer loyalty and demonstrate environmental responsibility, helping brands improve customer loyalty and build long-term trust.
Brands like Patagonia, Lululemon, and IKEA are already piloting resale programs that give used items a second life. This isn’t fringe. It’s the new mainstream. Swapping plastic packaging for more sustainable alternatives is another step brands can take to reduce waste and support circularity.
Pro tip: Create a branded “like new” collection and route eligible returns there instead of the liquidation abyss.
TL;DR: Stop Offsetting, Start Optimizing
If your entire returns sustainability strategy hinges on buying carbon credits, it’s time for a reboot.
Ecommerce brands have a huge opportunity to lead by:
- Reducing returns in the first place
- Routing them smarter and shorter
- Repurposing returns into value
- Implementing infrastructure that supports circular commerce
And you don’t need to be a $1B DTC darling to do this. Start small. Automate smarter. Ask better questions.
Because no amount of offsets will fix a broken process.
Frequently Asked Questions
How can ecommerce brands reduce return-related carbon emissions without offsets?
By using regional return hubs, minimizing return shipments through virtual try-ons or better sizing tools, and refurbishing items locally instead of reshipping them.
Why are carbon offsets considered greenwashing by some experts?
Because many offsets don’t reduce emissions at the source, they often act as a license to pollute rather than driving systemic sustainability improvements.
What are practical alternatives to carbon offsets for online retailers?
Implementing smart return routing, peer-to-peer resale, local drop-off partnerships, and clearer product education can meaningfully reduce returns emissions.
Do returns really make a big environmental impact?
Yes, especially when returns are shipped back, repackaged, restocked, or discarded. Each step contributes to carbon output, waste, and energy use.
How can ecommerce brands make their returns policy more sustainable?
Start by making returns frictionless but intentional: require reason codes, incentivize exchanges, offer local return options, and prioritize reuse or donation of returned items.
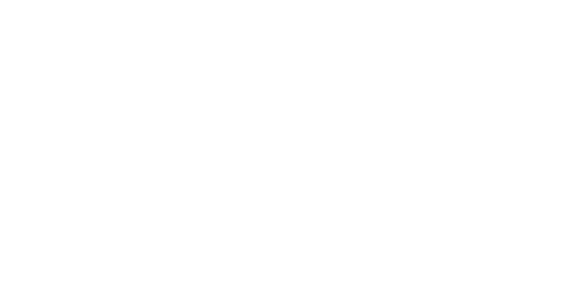
Turn Returns Into New Revenue
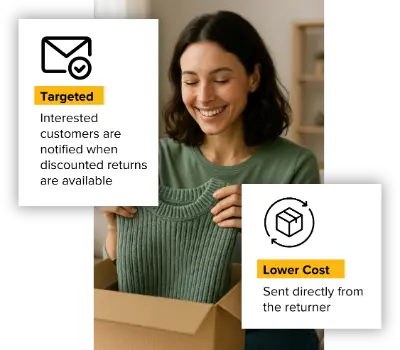
Why Temperature-Controlled 3PL Fulfillment Services Is Hot
In this article
6 minutes
- Why Brands Are Getting Serious About Temperature-Controlled Warehousing
- Four Ranges, Endless Requirements
- The Cold Storage Supply Chain Is Booming
- When Is Controlled Warehousing the Right Move?
- Key Benefits of Temperature-Controlled 3PL Fulfillment
- What to Look for in a Temperature-Controlled Facility
- Final Thoughts
- Frequently Asked Questions
So here’s the deal: not all products like to chill the same way. Some want crisp air. Others prefer it mild. And then there are the divas, like cheese, chocolate, and pharmaceuticals, that absolutely must stay within a consistent temperature range or things go sideways fast. Enter the world of temperature-controlled 3PL fulfillment services, where warehouses become climate whisperers and storage becomes science.
And let’s be honest, if you’re shipping temperature-sensitive products without the right temperature control setup, you’re flirting with spoilage, recalls, and angry emails. No one wants that.
Why Brands Are Getting Serious About Temperature-Controlled Warehousing
Blame it on the rise of DTC food, supplements, skincare, and all those perishable goods showing up on doorsteps. Ecommerce has exploded into categories that used to be strictly brick-and-mortar. Now everyone’s shipping salsa, serum, and medicinal products, and they all demand different temperature ranges and humidity levels.
That’s where temperature-controlled warehousing steps up. It’s not just about slapping an AC unit in the corner and calling it a day. A true climate-controlled warehouse is a carefully calibrated environment, with everything from refrigeration equipment to humidity control, air conditioning, and yes, even sandwich panels to regulate insulation.
Think of it like this: the temperature-controlled warehouse maintains product integrity the way a museum maintains art. It’s protection. It’s preservation. It’s essential.
Four Ranges, Endless Requirements
Let’s talk numbers. Most temperature-controlled facilities operate within four different temperature ranges:
1. Frozen (-10°F to 0°F): For ice cream, frozen meats, and products that prefer sub-zero vibes.
2. Refrigerated (33°F to 40°F): Think produce, pharmaceutical products, food grade items, and alcoholic beverages that demand cool-but-not-frozen conditions.
3. Ambient storage (50°F to 70°F): This is your standard controlled environment, great for supplements, makeup, or dry snacks.
4. Room temperature with humidity control: Often overlooked but critical for chocolate, electronics, and other temperature-sensitive goods.
Without proper temperature monitoring, one spike in heat or dip in cold air, and your stored goods could be toast. Literally. Improper storage doesn’t just shorten shelf life, it can lead to product quality issues, regulatory compliance headaches, and, worst-case scenario, a full-blown recall.
The Cold Storage Supply Chain Is Booming
We’ve all heard of the cold chain, but the spotlight on cold storage really intensified during the pandemic. Vaccines, fresh produce, and meal kits made everyone realize how fragile product integrity can be when temps aren’t dialed in just right.
Now that ecommerce has leaned hard into consumables, the need for temperature-controlled warehouse facilities isn’t just for Big Pharma or Big Food. Even indie brands selling elderberry syrup or adaptogen smoothies need safe storage that meets safety standards.
And that’s where 3PLs with temperature-controlled warehousing solutions come in hot (and cold). They’re building out storage space with energy consumption top of mind, balancing optimal storage with sustainability. It’s a delicate dance, keeping products stored safely while not blowing up the power bill.
When Is Controlled Warehousing the Right Move?
If you’re shipping anything that falls under sensitive products, perishable products, or items with “store below 72°F” on the label, yes, it’s time. That includes:
- Food products (fresh, frozen, or fancy)
- Pharmaceutical products
- Alcoholic beverages (yes, some spoil)
- Temperature sensitive goods like vitamins, probiotics, and CBD
- High-end cosmetics and skincare with active ingredients
- Specialty beverages, dairy alternatives, etc.
Look, there’s no one-size-fits-all in fulfillment. But if your goods don’t like high temperatures, or they melt, separate, rot, or grow fur in transit, temperature controlled storage isn’t optional. It’s critical.
Key Benefits of Temperature-Controlled 3PL Fulfillment
Here’s what a solid temperature controlled warehousing partner brings to the table:
- Consistency. A climate-controlled setup isn’t just cool sometimes. A good 3PL keeps a consistent temperature 24/7 using smart sensors, alarms, and responsive temperature monitoring systems.
- Flexibility. Need 1,000 square feet today and 10,000 next month? The right provider scales storage units and square footage with your seasonal swings.
- Regulatory compliance. Whether you’re dealing with FDA, USDA, or international guidelines, these folks help ensure compliance so you don’t get flagged or fined.
- Product quality. When your stored goods arrive fresh, intact, and ready to use, your customers notice. And so do your reviews.
- Lower risk. No more worrying about improper storage, spoiled batches, or losing a pallet because someone didn’t close the fridge door right.
What to Look for in a Temperature-Controlled Facility
Not all warehousing solutions are created equal. If you’re shopping for a 3PL, ask the awkward questions:
- What temperature ranges do they support?
- Can they offer different temperature zones in the same facility?
- Do they offer cold chain tracking or just ambient delivery?
- How often do they inspect and recalibrate their refrigeration equipment?
- What’s their backup power situation if temperatures rise unexpectedly?
Oh, and don’t forget the nerdy stuff, like expansion valves, airflow testing, and environmental conditions reporting. It’s not sexy, but it matters.
Final Thoughts
As ecommerce keeps moving into categories like wellness, food, and pharma, temperature-controlled warehousing needs are becoming the norm, not the niche. A few degrees can make or break a customer experience. A few missed requirements can sink a whole product launch.
So if you’re scaling a brand that relies on product integrity, get serious about your controlled warehousing strategy. Because when it comes to sensitive goods, the wrong warehouse is worse than no warehouse at all.
And if you’re still storing collagen gummies in your garage, well, it’s time to upgrade.
Frequently Asked Questions
What is temperature-controlled warehousing, and why does it matter?
Temperature-controlled warehousing is a storage solution that keeps goods within specific temperature and humidity ranges. It protects temperature-sensitive products from spoilage, ensuring quality, safety, and compliance across the supply chain.
Which products require temperature-controlled storage?
Items like perishable food, pharmaceutical products, skincare, supplements, and alcoholic beverages often need controlled temperatures to maintain product integrity and shelf life.
What temperature ranges are used in temperature-controlled warehouse facilities?
Most facilities operate within four different temperature ranges: frozen (-10°F to 0°F), refrigerated (33°F to 40°F), ambient (50°F to 70°F), and room temp with humidity control.
How does temperature-controlled warehousing support regulatory compliance?
By maintaining a consistent temperature range and offering detailed temperature monitoring, controlled facilities help brands meet FDA, USDA, and food safety standards.
Can a 3PL offer both ambient storage and cold chain solutions?
Yes. Many modern 3PLs provide flexible temperature-controlled warehousing solutions that include cold storage, ambient zones, and climate-controlled spaces, all under one roof.
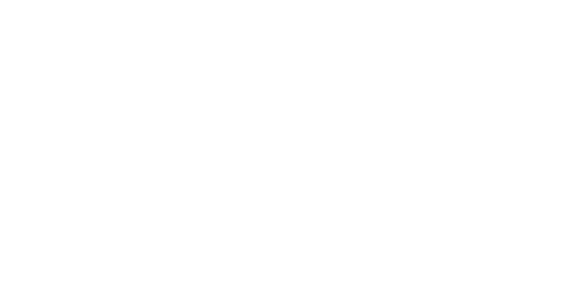
Turn Returns Into New Revenue
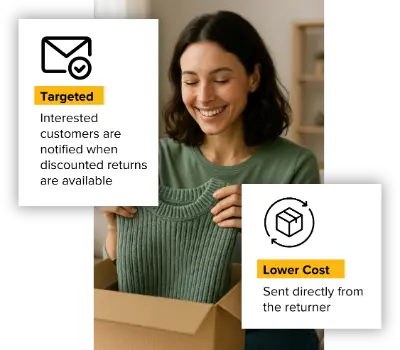
Rich Returns & Exchanges: Advantages and Disadvantages
Rich Returns & Exchanges is a Shopify app designed to automate returns and exchanges for merchants, with a special focus on integration with the Shop mobile app. In other words, it’s a commerce merchant’s tool to let customers initiate returns/refunds or exchanges smoothly on mobile and web. The app promises a “mobile-first experience” where customers can start returns right from the Shop App (Shopify’s shopping app) at checkout. Behind the scenes, Rich Returns provides an intuitive, self-service returns portal and label generation system, plus analytics to manage refund and exchange rules. In practice, many Shopify stores use it to centralize returns: it pulls order data directly from Shopify, simplifies refunds (even by issuing store credit), and tracks everything in a unified dashboard.
What Rich Returns Does Well
On the features side, Rich Returns covers the expected bases of a modern returns tool. It offers a custom-branded returns portal (hosted on the merchant’s site) where customers see their order, select items to return or exchange, and choose a refund method (original payment, store credit, etc.). The app automatically generates prepaid return labels from over 100 carriers worldwide; for example, FedEx, UPS, USPS, DHL, etc., so customers only need to print labels and drop off packages. Rich Returns even provides pre-filled return labels, eliminating the need for shoppers to enter address details, which users say “saves a lot of time and effort.” Email notifications are sent out at key milestones (return received, refund issued, etc.) to keep customers informed. A particularly unique advantage is the tight Shop App integration: merchants can let shoppers handle returns directly via Shopify’s mobile Shop app, creating a seamless, “mobile-first experience” in line with modern commerce. This means returns are visible to the customer just like any order, boosting transparency.
For merchants, Rich Returns provides automation rules and insights. You can set up conditional exchange suggestions (so if an item isn’t working, the system can prompt an exchange offer instead of a refund) to help “recapture lost revenue”. The app can automatically apply basic refund or exchange policies, and even offer discounted shipping labels if connected to certain apps (e.g., EasyPost). It supports data syncing with Shopify and common CRM tools (e.g., Intercom, Klaviyo) so that returns data and analytics flow into a merchant’s dashboard. According to app store details, the Standard plan ($19/mo) includes features like 10 free returns per month, a branded portal, and automated labels. Higher plans unlock multi-language support and advanced rules. Overall, many review snippets highlight responsive support and ongoing new features; one user said the team is “constantly improving and adding new features”. Rich Returns aims to improve customer satisfaction by making returns frictionless, ultimately helping brands build loyalty and scale up. In short, its strengths include a polished user interface, a built-for-Shopify architecture, and a clear focus on retaining revenue through exchanges and store credit.
Where Things Fall Apart
On the downside, a few limitations emerge. A prominent complaint is limited multi-language support. One Shopify reviewer gave low marks, saying: “App does not really support multi-language. Very poor implementation with limitations.” They noted some parts of the interface were not fully localized. In today’s global market, that can be a drawback for brands selling in multiple regions. Another issue is rich media: the same review mentioned that including photo (and video) uploads in the return form requires an extra paid add-on, and base support is lacking. In other words, if a customer needs to show a picture of a defect, Rich Returns’ basic plan doesn’t cover it; that feature must be purchased separately. A few merchants also found the app’s feature set “quite basic” for complex returns workflows: as one put it, it’s “not made as a platform, because every manual interaction has to be handled through another tool or Shopify.” This suggests that while core refund/exchange flows are covered, anything outside those (e.g., special RMA review processes) might require manual work or another system.
Some support issues have surfaced, too. Though many five-star reviews praise the team’s responsiveness, at least one user reported slow or “standard answers” that didn’t solve problems. This mirrors AfterShip’s feedback in a way: good support is not always guaranteed. Pricing can be another pain point for growing merchants. Only the Standard plan is very low cost; volume fees kick in after 10 returns per month. If a shop has hundreds of returns, the cost can climb, and some users express frustration at ongoing per-return charges. That said, Rich Returns is generally seen as affordable for what it offers.
Smaller Gaps and Missing Features
In terms of integrations, Rich Returns supports carriers through apps like EasyPost/Shippo (so effectively 100+ carriers) and connects to Shopify natively. It lacks dedicated Shopify Plus or alternative platform integrations, but it doesn’t need to since it’s Shopify-centric. We should note, however, that as a younger app (launched in 2019, with about 80 reviews), it does not have the decades-long pedigree of older systems. Some advanced features, like returns consolidation or very granular automation, are still evolving.
Verdict: Built for Shopify Simplicity, But Light on Power Features
Rich Returns is a solid choice for Shopify merchants who want a modern, mobile-friendly returns system deeply integrated with Shopify data and the Shop app. Its advantages include a responsive interface, exchange incentives to hold onto sales, and automated return label creation from many carriers. Support and user reviews are generally positive, which is notable given some apps’ history of ignoring merchants. However, the drawbacks, such as limited languages, the need to pay extra for media uploads, and basic (non-enterprise) workflows, mean it may not suit large global brands or very complex returns needs. In practice, Rich Returns tends to be praised for ease of setup and ongoing improvements, but critics warn about the absence of deeper customization.
For U.S. ecommerce operators weighing returns solutions, Rich Returns compares favorably to standard options (like AfterShip), but alternatives exist. For example, Cahoot’s peer-to-peer returns solution can dramatically reduce shipping costs by routing returns directly from the returning customer to the next purchasing customer. In any case, Rich Returns achieves its goal of “saving time” and boosting revenue via exchanges, yet it’s important to verify that its features (multi-language, integrations, any extra fees) align with your store’s scale and customer base before committing.
Frequently Asked Questions
Is Rich Returns only for Shopify?
Yes. It’s built specifically for Shopify merchants, with deep native integration and support for the Shop App. It’s not compatible with other ecommerce platforms.
Does it support photo uploads for return claims?
Not by default. Media uploads like photos or videos require a paid add-on. If your returns workflow relies on image-based verification, you’ll need to factor that into your budget.
Can Rich Returns handle exchanges automatically?
Yes, to a point. It supports exchange flows and can automatically suggest alternate items or offer store credit, helpful for saving the sale rather than losing it to a refund.
Is there multi-language support for international customers?
Sort of. Higher-tier plans include limited multi-language support, but some merchants report that localization is incomplete or poorly implemented.
What sets Rich Returns apart from other returns apps?
Its biggest strength is simplicity, especially for Shopify users. It’s easy to install, mobile-friendly, and offers a polished UI. That said, it may not have the depth or flexibility needed by large, complex operations.
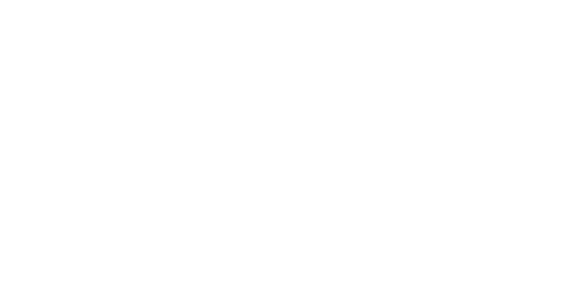
Turn Returns Into New Revenue
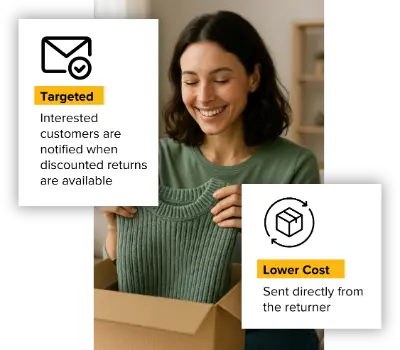
AfterShip Returns Management Solution: Advantages and Disadvantages
AfterShip’s Returns platform (often called AfterShip Returns Center) is a post-purchase tool that lets online retailers manage all customer returns and exchanges through a branded returns management portal that centralizes all return-related activities. In theory, it streamlines the entire returns process, from customer self-service returns to automated label generation, promising to “ensure a happy post-purchase experience”. The service integrates with major carriers (FedEx, USPS, Canada Post, etc.) to automatically generate return labels (prepaid shipping labels or merchant-paid labels) and track return shipments. In practice, many merchants praise its automation and analytics, but a significant number also report pain points with workflow and support. We’ll dig into the key features and then highlight the notable drawbacks, focusing especially on the latter.
What AfterShip Does Well
One of AfterShip’s selling points is a custom-branded returns portal. Merchants can publish a returns page on their domain (using store branding and colors) where customers see the store’s return policy and submit returns requests. Shoppers just enter an order number and email on this branded returns page and initiate a return “in just a few clicks”. This self-service approach avoids the email back-and-forth of traditional returns. Customers pick items and reasons for return on-screen, then AfterShip can automatically generate RMA numbers and prepaid return labels for them. The platform even offers discounted USPS label rates and supports printless QR-code drop-offs at 300K+ locations (including Canada Post and Happy Returns drop-off kiosks) to make return shipping easier. Customers can simply print the prepaid label and attach it to the box for return shipping, following the clear shipping instructions provided by AfterShip. In short, AfterShip’s returns page and label generation aim to create a seamless returns experience: customers can “return products and exchange products via a branded returns portal”, reducing hassle and improving customer satisfaction. The ease of use means customers can simply print their return labels at home.
Importantly, AfterShip advertises strong automation and analytics. Its dashboard centralizes all returns requests, RMA requests, and shipping status updates, which in trials has cut handling time in half (“50% reduction in returns processing time”). Merchants can set routing rules and eligibility rules (for example, auto-approve returns for certain items or dates) to speed up the returns approval process. The system can automate repetitive tasks in the returns process, reducing manual effort. The system can automatically create exchange orders or process refunds based on these rules, freeing merchants from manual steps. It also tracks every return shipment’s returns status and triggers email status updates to reassure customers. All this data feeds into an analytics dashboard to gain visibility on return rates, label costs, process time, and other key metrics. The idea is that AfterShip not only “saves processing time” and “reduces costs” by automating manual tasks, but also helps “recapture revenue with product exchanges” and increase brand loyalty by treating returns as marketing opportunities. AfterShip Returns helps build brand loyalty by providing a positive post-purchase experience.
In practice, many users find AfterShip’s interface and setup quite intuitive. Merchants say the returns page looks clean and integrates well with their store, and carriers like UPS, FedEx, USPS (and even Google Shopping integration via US Postal APIs) work without extra apps. The Shopify/BigCommerce app plug-ins make installation straightforward, and AfterShip’s pre-built integrations cover most common ecommerce platforms.
AfterShip provides detailed information about each step of the returns process, including setup, tracking, and support. On the positive side, support for analytics and exchange incentives means good customers can be offered store-credit refunds (instead of a full cash refund) to “turn returns into repurchases”. The platform allows merchants to efficiently track all returns requests in one place, and each returns request is logged and processed through the portal. Refunds can be issued directly to the original payment method. All these features work together to improve customer satisfaction.
Make Returns Profitable, Yes!
Cut shipping and processing costs by 70% with our patented peer-to-peer returns solution. 4x faster than traditional returns.
See How It WorksSummary: What Makes AfterShip Stand Out (When It Does)
- Branded returns pages with custom styling
- Prepaid shipping labels with carrier integrations
- Supports prepaid labels for easy customer returns
- Rules-based automation (refund/exchange approval)
- Real-time tracking and return shipment visibility
- Basic analytics dashboard and reporting
- Discounted USPS rates and printless QR return options
- Seamless setup for Shopify, BigCommerce, and similar platforms
- Happy Returns partnership for boxless returns
Where Things Fall Apart
However, numerous drawbacks have emerged in real-world use. A frequent theme is customer support issues. Several merchants on Shopify’s app store and review sites describe “terrible support” and generic, unhelpful responses. One store owner wrote that “the biggest issue is the customer service: it is terrible. Every agent is copying and pasting generic answers that have nothing to do with the issue… I would stay away from this app”. Others echo this, saying support tickets are closed without resolution and that agents lack product knowledge. A Canadian user complained, “Useless Customer Support cannot provide any help with the issue… We will switch to another tool”. These reports suggest merchants sometimes face long delays or poor communication when things go wrong.
On the feature side, AfterShip’s returns processes can be too rigid for some workflows. One merchant noted it’s not possible to skip intermediary steps (e.g., approve → refunded) without creating a “received” state first. Others have pointed out that the system’s canned email templates can have grammar errors and cannot be fully edited, which hurts the brand experience. Integration is another concern: while AfterShip works well with its own family of tools, many users say “most of its integrations only support other AfterShip products”, so if your store uses third-party warehousing or custom CRMs, you might find the returns center’s connectivity limited.
When AfterShip’s integrations fall short, merchants may face all the hassles of managing returns across multiple platforms, increasing complexity and manual work. In practice, some customers must manually upload prepaid labels if their preferred carrier isn’t supported, or use multiple platforms to process returns. In short, despite handling “all the returns requests” through one portal, a retailer may still end up juggling separate tools for complex returns flows.
Pricing and user policies have also disappointed some long-time users. AfterShip offers a free tier (a small number of returns per month) and several paid plans, but several reviews mention unexpected charges and changes. For example, one complaint said AfterShip abruptly changed to a per-user billing model and logged them out of the app without notice, calling the move “unethical and totally shameful”. Another user reported that after a recent update, “nothing is working like before”, the team couldn’t generate return labels and had to recreate accounts, effectively paying for access again. Others mention they can’t bundle all return shipping charges into a single monthly invoice, leading to confusion. These anecdotes suggest that policy changes can catch merchants off guard, adding hassles and potential “lost revenue” if returns are delayed.
Privacy concerns have even been raised: one merchant warned that AfterShip might store outdated customer emails in its database, which “violates US and EU laws”. While AfterShip responded that it respects privacy, such claims highlight merchant unease about data handling.
Finally, usability gaps remain. Some merchants find AfterShip’s portal lacking in multi-language support (despite international carrier integration) and in rich return options. A notable review said the app is “quite basic… every manual interaction has to be handled through another tool or Shopify”. Others wanted a built-in photo or video upload for returns (especially helpful for defect claims), but Rich Returns (not AfterShip) is mentioned for that. In AfterShip’s case, you can only upload photos in a limited way via the RMA management, which some users find inadequate.
Convert Returns Into New Sales and Profits
Our peer-to-peer returns system instantly resells returned items—no warehouse processing, and get paid before you refund.
I'm Interested in Peer-to-Peer ReturnsSummary: Smaller Gaps and Missing Features
- No peer-to-peer returns or next-generation solutions
- No in-store returns workflows (omnichannel support is light)
- No deep integration marketplace beyond core platforms
- Photo/video documentation is not built in by default
- Limited support for multi-language/localization
- Email templates can’t be fully customized on all tiers
- Returns policy customization and related workflow/routing rules are limited
Verdict: Feature-Packed and Familiar, But Support and Flexibility Fall Short
AfterShip Returns & Exchanges provides a robust automated returns solution with branded pages, multi-carrier label support, and flexible return rules, all aimed at “improving customer satisfaction” and “saving time”. When it works well, it does reduce the hassles of returns for both merchants and shoppers. However, many merchants report frustrations: particularly poor customer support, occasional system bugs (e.g., label generation failures), and unexpected pricing changes. Integration can also be a double-edged sword: the tight AfterShip ecosystem means great performance with built-in carriers, but limited options if you rely on other services.
In summary, AfterShip Returns Center is a mature, feature-rich portal for managing returns and exchanges in ecommerce. It excels at automating routine tasks (like label generation and status updates) and can truly “save processing time” and recover revenue through exchanges. Yet its disadvantages, chiefly support headaches and some workflow inflexibility, are significant for many merchants. If you value a wide integration network and 24/7 responsive service, be prepared for trade-offs. For U.S. brand operators looking at alternatives, consider that newer solutions like Cahoot’s peer-to-peer network promise to cut shipping costs by matching returned items to new buyers in-market. In short, AfterShip delivers many powerful returns features (including branded returns pages and automated carrier label generation), but its real-world cons, notably support and integration gaps, can leave customer satisfaction hanging in the balance.
Frequently Asked Questions
Does AfterShip Returns work with all carriers?
Not all of them. AfterShip supports major carriers like USPS, FedEx, UPS, and Canada Post, but for anything beyond that, merchants may need to manually upload return labels or rely on third-party tools.
Can customers submit return requests directly from my website?
Yes! AfterShip lets you publish a branded returns page where shoppers can initiate returns “in just a few clicks” using their order number and email.
What kind of automation does AfterShip offer for returns?
AfterShip includes basic automation rules, like auto-approving returns or triggering refunds based on eligibility. It also handles label generation and sends email status updates to customers automatically.
Are there hidden fees or plan limitations I should be aware of?
Several merchants have reported unexpected billing model changes and confusion around per-user charges or return volume tiers. It’s a good idea to read the fine print and monitor invoices.
How does AfterShip handle support?
Support is a mixed bag. Some users have good experiences, but others report generic responses and unresolved tickets. If hands-on support is critical, this might be a weak spot.
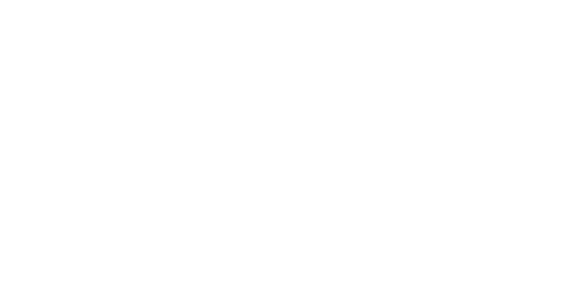
Turn Returns Into New Revenue
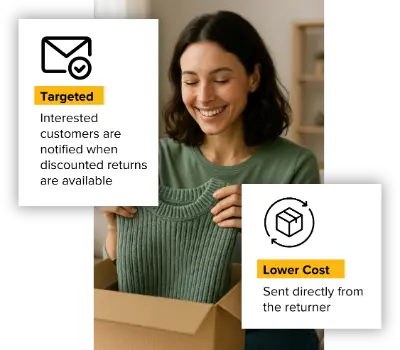