Cross-Docking: Benefits, Types, and Best Practices Explained

Last updated on April 01, 2025
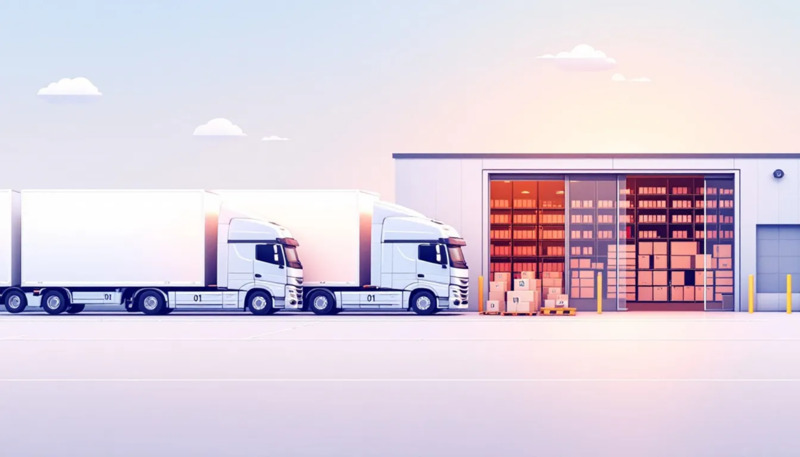
In this article
18 minutes
- Key Takeaways
- Understanding Cross-Docking
- Advantages of Cross-Docking
- Cross-Docking vs Drop Shipping
- Cross-Docking vs Direct Shipment
- Cross-Docking vs. Traditional Warehousing
- Types of Cross-Docking
- Cross-Docking Facilities
- Challenges and Solutions in Cross-Docking
- Common Categories and Industries That Use Cross-Docking
- Best Practices for Effective Cross-Docking
- How Cahoot Supports Cross-Docking: A Practical Example
- Summary
- Frequently Asked Questions
Cross-docking is a logistics strategy that transfers products directly from inbound to outbound shipments, reducing storage time and costs. This method speeds up the supply chain and enhances delivery efficiency. In this article, you’ll learn about the benefits, types, and best practices of cross-docking.
Key Takeaways
- Cross-docking enables the rapid transfer of goods from inbound to outbound transport, minimizing storage times and reducing warehousing costs.
- This logistics strategy significantly enhances supply chain efficiency, offering benefits such as cost savings, improved inventory management, and streamlined delivery processes.
- Effective implementation of cross-docking requires timely coordination between stakeholders, robust scheduling, and continuous improvement practices to address logistical challenges.
Understanding Cross-Docking
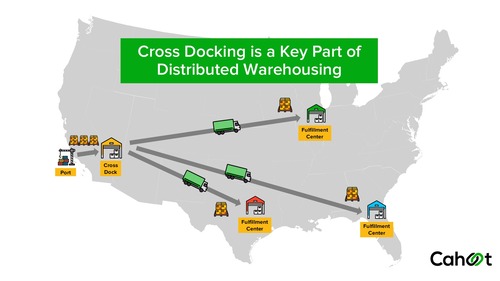
Cross-docking is a logistics process that minimizes storage and handling time by directly transferring products from inbound shipments to outbound transport. The primary goal is to reduce the time products spend in the supply chain, enhancing delivery efficiency and cutting warehousing costs. This method involves various types, such as pre-distribution, post-distribution, and continuous approaches, each supporting specific logistical needs, including Cross-docking services.
At the core of cross-docking lies in its ability to streamline the shipping process, ensuring that products move swiftly through the supply chain. Minimizing storage time leads to less inventory handling, less capital tied up in inventory for less time, and reduced warehousing costs for businesses.
What is Cross-Docking?
Cross-docking is a logistics process where products from a supplier or manufacturing plant are distributed directly to a customer or retail reseller with minimal handling and storage time. Unlike traditional warehousing, where goods are stored for extended periods, cross-docking facilities are designed for rapid movement and redistribution of goods. This approach ensures that products are sorted and dispatched almost immediately after their arrival at a logistics facility.
The primary goal of cross-docking in supply chain management is to speed up the supply chain process by reducing the need for long-term storage and minimizing handling costs. Cross-docking facilities, often referred to as cross-docks, are strategically located hubs that facilitate the direct transfer of goods from inbound to outbound transport.
Utilizing a specialized layout that minimizes storage time allows cross-docking warehouses to ensure efficient redistribution of products. This method significantly differs from traditional warehousing, focusing on fast movement and less inventory handling. The efficiency gained through cross-docking operations can lead to substantial cost savings and improved supply chain performance.
Key Steps in the Cross-Docking Workflow
The cross-docking workflow involves several key steps designed to ensure the swift movement of goods through the supply chain. It begins with receiving goods, where products are unloaded from inbound trucks at the receiving dock. This step involves minimal handling, allowing items to be quickly sorted.
Once the goods are received, they are sorted according to orders or delivery routes and redirected for immediate delivery. This sorting process is important for consolidating shipments and ensuring that products are directed to their correct destinations. The efficiency of this step is determined by the strategic layout of cross-docking facilities, which minimizes the distance goods need to travel within the warehouse. Finally, the sorted products are loaded onto outbound vehicles for delivery to their final destinations.
Advantages of Cross-Docking
Cross-docking offers numerous advantages that make it an attractive logistics strategy for many businesses. One of the primary benefits is cost savings, as it reduces the need for extensive warehousing and minimizes handling and storage expenses by cutting down on storage time and the number of human touches.
Another major advantage of cross-docking is improved efficiency. Facilitating the swift movement of goods from inbound to outbound shipments enhances delivery speed and reduces lead times. This approach also improves inventory management by minimizing excess inventory and reducing the risk of overstocking or stockouts. Together, these benefits contribute to a more streamlined and cost-effective supply chain operation.
Cost Savings
Cross-docking can lead to significant cost savings for businesses by reducing various expenses associated with traditional warehousing. Labor costs are decreased since products require less handling, leading to a reduced need for workforce management, resulting in cost savings in supply chain operations. Additionally, lower utility expenses result in more economical storage costs. By minimizing long-term storage and excessive handling, cross-docking helps businesses achieve a more cost-effective logistics strategy.
Improved Efficiency
Cross-docking enhances efficiency, allowing goods to move swiftly to their destinations. Allowing products to be sorted and dispatched almost immediately drastically cuts down on delivery times.
Regularly evaluating cross-docking processes helps identify areas for further simplification and even more efficiency. This continuous improvement loop ensures that the cross-docking operation remains streamlined and effective, ultimately leading to improved service levels and reduced costs.
Enhanced Inventory Management
Cross-docking minimizes the need to keep excess inventory to meet fulfillment expectations, helping businesses maintain optimal stock levels and reduce the chance of overstocking and stockout situations.
Machine learning and genAI applications in cross-docking can significantly improve demand forecasting by analyzing historical shipping data, real-time market trends, and geopolitical events to optimize inventory levels and capital spending. Leveraging advanced technologies to optimize inventory management ensures timely deliveries and reduces warehousing costs.
Cross-Docking vs Drop Shipping
Cross-docking and drop shipping are two distinct logistics strategies, each with its own set of advantages and disadvantages. Cross-docking focuses on the immediate transfer of goods between inbound and outbound transport, reducing storage duration and lowering costs associated with warehousing and handling. It improves supply chain efficiency by minimizing the need for long-term storage and reducing inventory touches.
On the other hand, drop shipping allows businesses to reduce the initial investment and ongoing costs associated with buying and holding inventory by having suppliers ship products directly to customers after the purchase is made. While this method also eliminates the need for inventory management and storage, it can lead to longer delivery times and increased transportation costs, which erodes margins and risks long-term customer loyalty typically (at least partially) attributed to fast and free shipping.
Cross-Docking vs Direct Shipment
When comparing cross-docking with direct shipment, both methods offer unique benefits and challenges. cross-docking allows fulfillment centers to ship internationally without altering their established processes, making it a versatile option for global logistics. However, one major drawback is that it can extend transit times, leading to longer customer wait times for receiving orders.
Direct shipment, or hubless shipping, allows retailers to fulfill orders directly from their warehouses to international customers, bypassing the need for a cross-dock center. This method can reduce transit times but may require more complex logistics management and higher inventory holding costs.
Cross-Docking vs. Traditional Warehousing
Cross-docking and traditional warehousing represent two different approaches to logistics management, each with its own set of advantages and disadvantages. The cross-docking process prioritizes rapid movement of goods, significantly decreasing the time required to get products from suppliers to customers. This method generally incurs lower operational costs related to physical storage space and inventory management compared to traditional warehousing.
However, traditional warehousing allows for better adaptability to changes in demand and inventory, serving as a buffer to manage variability. This flexibility can be crucial in industries with fluctuating demand patterns. And taking advantage of economies of scale and negotiating bulk purchases increases margins and profitability. But the extended margins on one side may be lost to fixed operating costs on the other, so businesses should understand the strengths and weaknesses of each approach and choose the one that best aligns with their operational goals and customer needs.
Types of Cross-Docking
Cross-docking can be categorized into various types, each serving distinct logistical needs. The primary types include pre-distribution, post-distribution, and continuous cross-docking. Each type is defined by the timing of product sorting and the specific logistical requirements it addresses.
Pre-distribution cross-docking involves sorting goods before they arrive at the distribution center, while post-distribution cross-docking sorts products after they reach the facility. Continuous cross-docking emphasizes an uninterrupted flow of goods through the facility, ensuring rapid transfers and meeting consistent product demand.
Additionally, consolidation and deconsolidation methods facilitate direct product shipment without prior storage, optimizing fulfillment efficiency.
Pre-Distribution Cross-Docking
Pre-distribution cross-docking involves sorting goods according to their final destination before they arrive at the distribution center. In this approach, products are sorted and designated for their final destinations before arriving at the cross-dock facility. This method streamlines logistics by ensuring timely delivery based on prior customer demand.
Organizing products before they arrive at the distribution center minimizes handling and storage time, enhancing overall supply chain efficiency. This approach is particularly beneficial for industries with predictable demand patterns and well-defined delivery routes.
Post-Distribution Cross-Docking
In post-distribution cross-docking, the final destinations of goods are determined after they have reached the distribution center. This method involves sorting and allocating products to their next destinations based on real-time demand and supplier decisions. Providing more flexibility in determining shipping destinations allows post-distribution cross-docking to adapt to changing market conditions and customer needs.
This approach allows suppliers to make informed decisions about product allocation, ensuring optimal delivery routes and minimizing excess inventory. Post-distribution cross-docking is ideal for industries with variable demand patterns and the need for agile logistics management.
Continuous Cross-Docking
Continuous cross-docking is a logistics strategy that emphasizes an uninterrupted flow of goods through the facility. This process minimizes storage time as goods move directly from inbound to outbound transport without intermediate storage. Maintaining a steady flow of products facilitates rapid transfers and meets consistent product demand in continuous cross-docking.
This approach is particularly effective for high-volume industries with steady demand, such as retail and ecommerce. Continuous cross-docking ensures that products are always on the move, reducing the need for long-term storage and maximizing supply chain efficiency.
Consolidation and Deconsolidation
Consolidation and deconsolidation cross-docking are methods that facilitate direct product shipment without prior storage, enhancing transportation efficiency. In consolidation cross-docking, multiple smaller shipments are temporarily set aside and merged into a larger shipment for more efficient transport. This method reduces transportation costs by maximizing load capacity and minimizing the number of trips required.
Deconsolidation cross-docking, on the other hand, entails breaking down large shipments into smaller, easier-to-handle deliveries for further distribution. This approach is beneficial for distributing products to multiple locations or end-users.
Both methods involve some level of product handling in the warehouse, but they significantly reduce long-term storage needs and improve overall supply chain efficiency.
Cross-Docking Facilities
The design and infrastructure of cross-docking facilities play a decisive role in overall efficiency of operations. Optimizing the layout of these facilities can significantly reduce travel time and enhance material flow, ensuring that goods move swiftly from inbound to outbound shipments. Strategic layout design, including the placement of receiving docks and loading docks, is essential for minimizing the movement distance of goods.
Automation is another critical aspect of cross-docking facilities. Implementing automated systems for transferring goods can increase operational efficiency and reduce the risk of product damage. Improvements in infrastructure and technology, such as layout design optimization and automation, contribute significantly to the success of cross-docking operations.
Cross-Docking Terminals
A cross-docking terminal is a specialized facility designed for the swift movement and redistribution of shipments, differing significantly from a standard warehouse that is geared towards storing and managing inventory over a longer period. These terminals typically feature configurations like I-shaped or T-shaped layouts to facilitate numerous loading and unloading docks. Unlike traditional warehouses, cross-docking terminals have doors on both sides to streamline the unloading and loading process for efficient goods movement.
The primary focus of cross-docking terminals is to ensure rapid transfer and sorting of goods, prioritizing efficiency over long-term storage. A well-designed cross-docking facility should feature optimized layouts and adequate handling equipment to ensure efficiency.
Cross-docking terminals facilitate the quick turnover of goods and play a vital role in enhancing supply chain operations.
Role of Digital Technology
Digital technology plays a pivotal role in enhancing cross-docking operations by enabling real-time tracking and management of inventory and locations within the facility. Implementing tracking systems allows for early identification of issues, which is crucial for maintaining quality throughout the cross-docking process. Automated sorting systems are integral in cross-docking to improve efficiency by minimizing manual sorting and reducing errors in the handling process.
Companies like Walmart employ autonomous robots and real-time data analytics to optimize cross-docking workflows in their distribution centers. Advanced communication technologies, such as cloud platforms and EDI, improve real-time data sharing, enhancing coordination among all parties involved in the cross-docking process.
These technological advancements are essential for maintaining smooth and efficient cross-docking operations.
Machine Learning and Analytics
Machine learning and analytics are powerful tools that can significantly improve the accuracy of demand forecasting and analytics processes in cross-docking. By analyzing historical shipping data and patterns, machine learning algorithms can optimize inventory levels, ensuring that products are available when needed while minimizing excess inventory.
This technology enhances the overall efficiency of cross-docking operations, leading to better supply chain management and improved customer satisfaction.
Challenges and Solutions in Cross-Docking
While cross-docking offers numerous benefits, it also presents several challenges that businesses must address to ensure successful implementation. One major challenge is the complexity of coordinating various stakeholders involved in the supply chain. Effective management of multiple stakeholders is essential to ensure precise timing and operations, as delays can disrupt the entire cross-docking program and lead to disappointed customers.
Another significant challenge is the high cost associated with setting up the necessary infrastructure for cross-docking operations. Investments in advanced sorting technologies and staff training can mitigate these expenses, but the initial supply chain costs can be substantial.
Additionally, maintaining stringent quality control is crucial to ensure product integrity and customer satisfaction. By addressing these challenges, businesses can optimize their cross-docking operations to be more robust, resulting in greater operational efficiency.
Coordination Complexity
Cross-docking requires effective management of multiple stakeholders to ensure precise timing and operations. Successful cross-docking relies on precise synchronization between inbound and outbound transportation schedules, which can be challenging to achieve. Maintaining real-time communication among all stakeholders helps ensure accurate information flow and timely decision-making in cross-docking operations.
Regular assessment of cross-docking processes is essential to identify areas for improvement and adapt to changing operational demands. By continuously evaluating and refining their cross-docking practices, businesses can overcome coordination complexities.
Infrastructure Costs
Depending on the volume needs of the business, setting up a cross-docking facility can incur substantial initial investments, particularly when incorporating advanced sorting technologies, but investments in technology and staff training can mitigate these expenses. Strategic planning and resource allocation help businesses reduce the financial burden of infrastructure needs and help to achieve long-term benefits.
Despite the high initial costs, cross-docking offers significant cost savings in the long run by reducing labor, storage, and management expenses. By minimizing long-term storage and excessive handling, cross-docking helps businesses achieve a more cost-effective business model.
Quality Control
Quality control is essential in cross-docking to ensure product integrity and customer satisfaction. The quick assessment of damage during unloading allows for immediate action on compromised products, maintaining high standards of quality throughout the cross-docking process. Implementing robust quality control measures helps businesses maintain the trust and satisfaction of their customers.
Regular monitoring and evaluation of quality control processes are crucial for identifying and addressing potential issues. Maintaining stringent quality control ensures that cross-docking operations remain efficient and reliable.
Common Categories and Industries That Use Cross-Docking
Cross-docking is widely used in various industries, particularly those dealing with perishable or time-sensitive items. The retail sector, for instance, utilizes cross-docking to enhance order speed and minimize inventory costs, ensuring quick delivery of goods to consumers. Fast-moving sectors like fashion, electronics, and groceries significantly benefit from cross-docking by meeting the demands for speedy delivery.
Other industries that leverage cross-docking include food and beverage, automotive, ecommerce, and healthcare. In the automotive industry, cross-docking supports Just-in-Time manufacturing, ensuring timely delivery of components and minimizing warehousing needs. Ecommerce companies also benefit from cross-docking by streamlining their supply chains, ensuring efficient logistics and rapid fulfillment.
Best Practices for Effective Cross-Docking
Effective cross-docking implementation relies on seamless collaboration between suppliers, manufacturers, and retailers to avoid disruptions. Timely coordination between inbound and outbound shipments is critical, as delays can disrupt the entire operation. Continuous communication and real-time updates among all parties involved ensure smooth and efficient cross-docking activities.
Implementing a well-defined management system and regularly evaluating cross-docking processes are essential for overcoming logistical challenges related to timing and space management. By following best practices, businesses can achieve successful cross-docking operations and enhance their supply chain efficiency.
Efficient Scheduling
Accurate shipment scheduling is vital to ensure timely arrivals and departures and minimize idle time at cross-dock facilities. Precise scheduling is critical in cross-docking to synchronize inbound and outbound shipments and prevent operational delays. Creating a well-planned transportation schedule ensures that inbound and outbound shipments are coordinated to avoid delays and maximize throughput.
Effective scheduling helps businesses maintain a steady flow of goods, reducing the risk of bottlenecks and enhancing overall supply chain efficiency. By investing in robust scheduling systems, companies can achieve significant planning and operational benefits in their cross-docking operations.
Real-Time Communication
Maintaining continuous communication between all parties involved is crucial for the smooth execution of cross-docking. Real-time communication ensures that any issues or delays are promptly addressed, minimizing the impact on the overall operation. Advanced communication technologies, such as cloud platforms and EDI, enable instant updates and coordination among suppliers, manufacturers, and retailers, enhancing the efficiency of cross-docking processes.
Fostering open and transparent communication channels ensures that all stakeholders are aligned and informed, leading to more effective and efficient cross-docking operations. Regularly updating and refining communication protocols is essential for maintaining high standards in cross-docking activities.
Continuous Improvement
Continuous improvement in cross-docking processes is key to maintaining efficiency and customer satisfaction. Regular evaluation of cross-docking practices helps identify areas for enhancement, contributing to overall efficiency and effectiveness. By continuously refining their operations, businesses can achieve faster product turnover and quicker order fulfillment, enhancing customer satisfaction.
Implementing a culture of continuous improvement ensures that cross-docking operations remain agile and responsive to changing market conditions. Regularly assessing processes and making necessary adjustments helps businesses maintain high standards in supply chain management and achieve long-term success.
How Cahoot Supports Cross-Docking: A Practical Example
Many Cahoot clients supplement their traditional warehousing and ecommerce order fulfillment operations with a cross-dock program. After setting up relationships with vendors, Sellers create large product catalogs and list the items across their sales channels. After the daily order cutoff time, (usually 5 or 6 pm local time), the list of SKUs and quantities are sent to the vendors as a purchase order where the order is picked and packed into a bulk shipment and delivered by the next morning or following day. The bulk delivery is unpacked, items are matched to orders, fulfilled same-day and handed over to carriers for final-mile delivery.
Many vendors that support these cross-docking relationships approve regional ambassadors as their go-to partners in those regions, but not in distant regions. By partnering with the Cahoot elastic warehousing network, new regions are opened up for those Sellers allowing them to ship and deliver orders faster across the nation, rather than limited to a particular region. New vendors become available, product catalogs grow and provide more opportunities for discoverability and sales, and Sellers increase revenue and profitability, besides reducing fulfillment expenses by outsourcing the remote fulfillment operations and improving margins even more.
Contact us to learn more.
Summary
Cross-docking is a powerful logistics strategy that offers numerous benefits, including cost savings, improved efficiency, and enhanced inventory management. By minimizing storage and handling time, businesses can achieve faster deliveries and reduce warehousing costs, leading to a more streamlined and cost-effective supply chain operation.
Successful cross-docking implementation requires careful planning, effective coordination, and continuous improvement. By following best practices and leveraging advanced technologies, businesses can optimize their cross-docking operations and achieve greater supply chain efficiency. As logistics and supply chain management continue to evolve, cross-docking will remain a vital strategy for businesses looking to enhance their operations and meet the demands of an increasingly competitive market.
Frequently Asked Questions
What is the primary goal of cross-docking in supply chain management?
The primary goal of cross-docking in supply chain management is to expedite the supply chain and fulfillment workflows by minimizing storage time and lowering handling costs. This approach enhances efficiency and responsiveness in product distribution.
What is cross-docking?
Cross-docking is an efficient logistics method that enables products to move directly from suppliers to customers or retailers with minimal handling and storage in between. This approach streamlines operations and reduces delivery times.
Which companies leverage cross-docking to streamline their operations?
Walmart, Toyota, and Lowe’s, among many others, all effectively utilize cross-docking to enhance their operational efficiency and reduce costs.
What are the advantages of cross-docking?
Cross-docking offers significant advantages such as expedited delivery times, minimized storage and transportation costs, and reduced labor expenses. Additionally, it lowers the risk of spoilage, damage, or theft due to limited handling of goods.
What is a cross-docking terminal?
A cross-docking terminal is a specialized facility focused on the rapid transfer and reallocation of shipments, in contrast to traditional warehouses that primarily store inventory for extended periods. This efficiency in handling logistics streamlines the supply chain process.
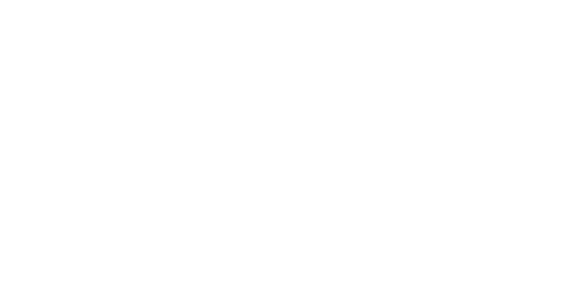
Up to 64% Lower Returns Processing Cost
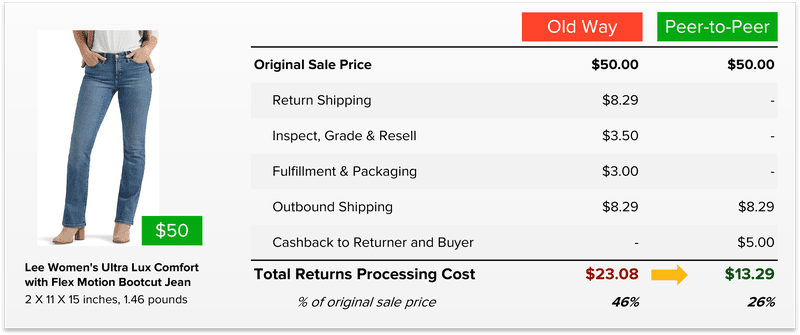