Next-Gen Warehouse Automation Software for Ecommerce: Fulfillment Efficiency

Last updated on March 19, 2025
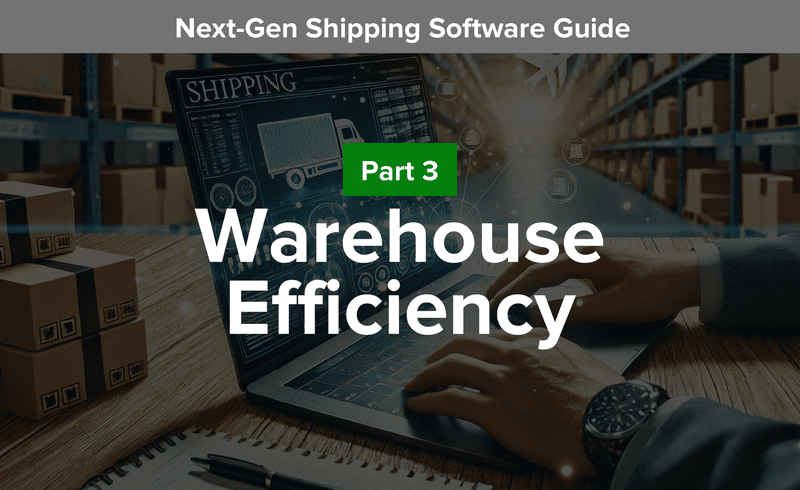
In this article
13 minutes
- Understanding Fulfillment Challenges
- Warehouse Efficiency: Supercharge Productivity for Your Team
- Automated Shipping Workflows with Warehouse Management Systems
- Making Large, Complex Orders Easy to Handle
- Optimizing Your Fulfillment Network and Carrier Management
- Summary: Why Next-Gen Shipping Software is a Game Changer
- Frequently Asked Questions
Ecommerce order fulfillment is more than just packing and shipping — it’s about precision, speed, and cost efficiency. Businesses that rely on outdated legacy systems often face delays, high labor costs, and manual errors, making it difficult to meet growing customer expectations.
Enter next‑generation warehouse automation software for ecommerce: designed to optimize every step of the fulfillment process. From intelligent order routing to real‑time tracking and automated cartonization, modern shipping software maximizes warehouse efficiency, reduces costs, and ensures seamless operations. By integrating smart automation, businesses can scale effortlessly while delivering faster and more reliable shipping experiences.
In this article, we’ll explore how shipping software enhances warehouse efficiency, minimizes fulfillment challenges, and empowers merchants to stay ahead in a competitive market.
Understanding Fulfillment Challenges
Fulfillment challenges can significantly impact a business’s ability to deliver products efficiently and effectively. Understanding these challenges is crucial to implementing effective solutions.
Manual Processes and Labor Costs
Manual processes can be a significant drain on resources, leading to increased labor costs, reduced productivity, and a higher risk of errors. Tasks such as manual data entry are not only time‑consuming but also prone to mistakes, which can cause delays and escalate costs. This is where automation solutions, like warehouse management systems (WMS), come into play. By automating repetitive tasks, a WMS can streamline operations, reduce the need for manual labor, and minimize errors. This not only cuts down on labor costs but also frees up your team to focus on more strategic activities that drive business growth.
Disconnected Software Programs and Missing Tracking Info
Disconnected software programs can create a fragmented fulfillment process, leading to missing tracking information and making it difficult to monitor and manage inventory levels, shipping, and delivery. This lack of integration can result in inefficiencies and errors that disrupt the entire supply chain. Implementing a seamless integration between software programs, such as a WMS and shipping software, can significantly improve visibility and control over the fulfillment process. With integrated systems, you can ensure that all parts of your operation are synchronized, providing real‑time updates and comprehensive tracking information. This not only enhances operational efficiency but also improves customer satisfaction by ensuring timely and accurate deliveries.
Warehouse Efficiency: Supercharge Productivity for Your Team
We’ve now discussed how shipping software needs features that help you simplify the complex new world of ecommerce. But Sellers are not just focused on simplifying operations inside their businesses. Pressure from the outside continuously bears down on them – whether it’s rivals on online marketplaces, multiple channels to market and sell on, or demanding customers.
Efficient shipping processes play a necessary role in enhancing productivity by automating tasks such as creating labels, tracking packages, and handling returns, ultimately leading to improved customer satisfaction.
And all this is happening amid a competitive labor market, where staffing has become expensive and challenging. It isn’t enough for an ecommerce shipping software to reduce operational complexity. It must do so with minimal human intervention and resources, allowing you to do more with less. Crucially, the software must unlock productivity gains for today’s small teams, enabling them to focus on high‑value work.
In the previous section, you might’ve seen that legacy software has features that can simplify operational complexity. However, those features are often painful and convoluted to implement by a small team of seasonal or part-time workers. We think there are 3 major areas where shipping software must streamline workflows efficiently:
- Does the software have humanless, autonomous automation across shipping workflows, or does it require constant babysitting?
- In a world with increasing basket sizes, can it unlock time savings for warehouse staff by automating packaging selection?
- Is the product easy for seasonal or part‑time workers to use, without specialized training?
In the coming sections, we’ll examine each of these areas, showing how legacy software drains productivity and how next‑generation shipping software reclaims time, boosts efficiency, and drives growth.
Automated Shipping Workflows with Warehouse Management Systems
Legacy Software – Labor Intensive and Painful
The most important tasks in shipping software are routing orders to fulfillment locations and identifying the cheapest shipping label.
Legacy shipping software uses manual, repetitive steps for printing labels. Typically, after logging in, you must:
- Open an order
- Fix address issues
- Identify which warehouse has the SKU in stock
- Assign a “Ship From” location based on the customer’s address
- Select packaging
- Rate‑shop across carriers and services one at a time
- Pick the cheapest service
- Print the label
- Repeat for the next order
Some of these steps can be automated through crude, hard-coded automation rules but those are time-consuming to configure and can still be inaccurate. A rule is needed for almost every single workflow. Here are some reasons why this process is so elaborate and painful:
- Automations in most legacy software require certain criteria to be defined. When orders meeting these criteria (for example, orders for a certain SKU) enter the system, the rule is triggered to execute certain actions (like assigning a certain carrier or service). But what are all these rules defined for? Their ultimate aim is to find the lowest-priced shipping label on every order. These rules simply trigger certain actions to occur, rather than rate shopping for the cheapest label by comparing carriers and services.
- Even the simple steps need a rule. For example, if you’re delivering to a residential address, then only certain services can be used – like FedEx Home Delivery, for example. A rule needs to be written to ensure this mapping is considered by the system. All this makes it enormously difficult to cut down the number of keystrokes and clicks.
- ShipStation’s ‘Auto-routing’ feature (still in Beta in 2025), only factors in which locations have a product and their distance from the customer before assigning orders to a fulfillment center. It still does not support the comparison of real-time shipping rates for each carrier and service to make a full and final, (accurate), decision.
In our estimation, it would take the average human over 5 hours to print labels for 1,000 orders!
And as we all know, a human is not a computer. When doing a repetitive task for such a long period of time, fatigue and the possibility of errors increase dramatically. It’s also worth asking – why should a human be engaged in such repetitive, low-value work all day long?
Next‑Gen Software – Humanless and Seamless
With next-generation shipping software, the difference is like night and day. The system intelligently compares warehouse locations, carriers, shipping services, inventory levels, and shipping supplies to instantly and automatically generate shipping labels for every single order, and integrating seamlessly with inventory management enhances efficiency and accuracy.
Here’s the sequence of steps to accomplish the same goal using Cahoot (after logging in):
- Verify the address corrections made automatically by the system
- Prints labels in bulk
The system automates many steps that legacy software doesn’t – it spots potential issues with addresses and makes suggestions to fix them, it only considers warehouses that have inventory available, it selects the smallest packaging that an order can fit into and ship safely, and it rate-shops that package weight and dimension across all carriers, services, and warehouses for the cheapest service.
It’ll take the average human just 15 minutes to print labels for 1,000 orders in Cahoot, and most of that time is waiting for the printer to finish its job. We’ve made a video where you can get a glimpse of how this works, and how we stack up against the popular legacy shipping software ShipStation (if you’d like to see a little more about how Cahoot compares to ShipStation, read our comparison here!) You can sit back and relax, knowing that the optimal selection was made for every single order using technology. You can also free up your time to work on other tasks that add more value to the bottom line. If you’re finding it difficult and expensive to hire more people, you can ensure that the people you do have are focused on the problems that matter the most.
You can see it in action, or read our ShipStation comparison to learn more.
Making Large, Complex Orders Easy to Handle
Legacy Software – Left to Humans and Heuristics
Legacy shipping software is mainly focused on one portion of the fulfillment workflow – printing shipping labels. In a world of rising basket sizes, merchants have complexity in other steps of the shipping process, including shipment packaging selection. Optimizing layout and staff allocation in a distribution center can significantly enhance shipping efficiency and reduce costs.
This is a common problem that customers of legacy software like ShipStation face. For complex orders that might require multiple boxes of various sizes, they are forced to enter the box dimensions manually each and every time based on the SKUs in the order. The customers from their community forum below are requesting a pull-down list of the common boxes they use so they can quickly make the selection rather than manually entering dims.
The customer is also highlighting a more important issue – they can add a set of boxes as a “base” in ShipStation. This feature aims to serve as a default that can be applied to most MLMQ orders. However, unless you’re lucky that most of your MLMQ orders consist of the same unique combination of SKUs, such a feature is pointless.
The list of automation rules that need to be written to map SKU combinations to boxes is dizzyingly long and involves having to figure out all the possible SKU permutations; impossible if your product catalog is any more than a couple dozen SKUs.
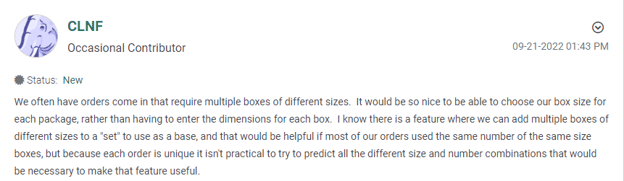
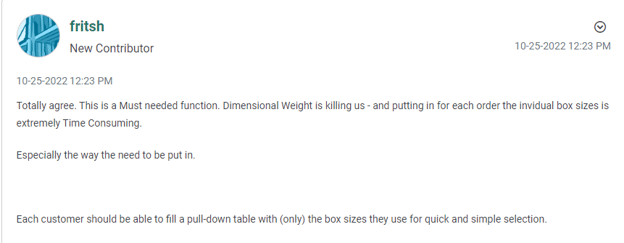
As the classic saying goes, customers are great at highlighting problems, but not identifying solutions. We think this is a big pain point that next-generation software already solves.
Next-Gen Software – Powered by Machine Learning for Warehouse Operations
Cahoot’s next-generation shipping software solves both of these problems. We don’t think the solution is a drop-down list, because you’re just replacing keystrokes with clicks. It’s still human effort and time.
Our software remembers the box selection you make the first time and applies it by default the next time regardless of how many SKUs and units of each are in the order. This ensures you’re freed up from repetitive manual entries and clicks.
We don’t believe the solution to picking the optimal box for every MLMQ order is an arbitrary default or crude automation rule. The Cahoot system uses breakthrough cartonization innovation to intelligently evaluate the space utilization for a group of items across all available boxes in stock and calculates the percent fit (% fit), making sure the most optimal box is automatically selected every time.
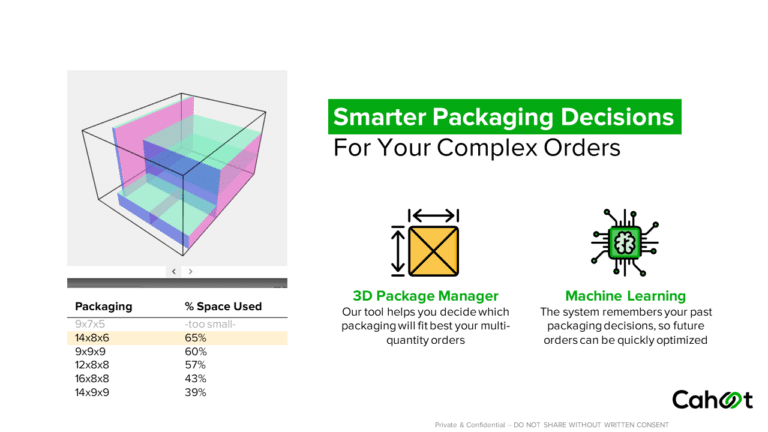
This frees your team from data entry and guesswork, letting them focus on higher‑value tasks that grow your business.
Optimizing Your Fulfillment Network and Carrier Management
Optimizing your fulfillment network and carrier management is crucial to ensuring efficient and cost-effective shipping operations.
Fulfillment Network and Carrier Performance Metrics
Monitoring fulfillment network and carrier performance metrics is essential for optimizing shipping operations. Key metrics—on‑time delivery rates, shipping costs, and customer satisfaction—provide insights into your fulfillment efficiency. Implementing a WMS offers real‑time visibility, enabling data‑driven decisions to optimize carriers, reduce costs, and improve delivery reliability.
By understanding challenges and optimizing your network and carriers, businesses can boost warehouse efficiency, cut costs, and elevate customer satisfaction through integrated, automated solutions.
Summary: Why Next‑Gen Shipping Software is a Game Changer
Traditional fulfillment systems struggle with modern ecommerce demands—high labor costs, fragmented software, and manual workflows. Next‑generation warehouse automation software transforms operations by automating workflows, optimizing packaging, and integrating sales channels.
Features like real‑time tracking, AI‑powered cartonization, and automated carrier selection let businesses scale without bottlenecks. Investing in the right software drives down costs, increases accuracy, and delivers a seamless fulfillment experience.
Learn more in our Next Generation Shipping Software Guide, Part 4: “Save Money With Ecommerce Shipping Software: Next‑Gen Solutions”.
Frequently Asked Questions
How does warehouse automation software improve ecommerce fulfillment?
Warehouse automation software streamlines fulfillment by automating order routing, label generation, and inventory tracking. This reduces errors, speeds processing, and optimizes carrier selection for faster, more cost-effective deliveries.
What are the key benefits of using shipping software for warehouse efficiency?
Shipping software enhances warehouse efficiency by automating label printing, integrating with multiple carriers, optimizing order packing, and providing real‑time tracking. These features reduce labor costs, minimize delays, and improve fulfillment accuracy.
Can warehouse automation software integrate with existing ecommerce platforms?
Yes. Most next‑generation warehouse automation solutions integrate seamlessly with platforms like Shopify, Amazon, Walmart, and eBay—synchronizing inventory, orders, and shipping updates in real time.
How does automated cartonization help reduce shipping costs?
Automated cartonization uses AI to select the best box size for each order, reducing dimensional weight fees and wasted space. This optimization lowers shipping costs and improves warehouse space utilization.
How do I choose the right warehouse automation software for my business?
Consider integration capabilities, ease of use, automation features, and scalability. Look for solutions supporting multiple carriers, intelligent order routing, and analytics for continuous optimization.
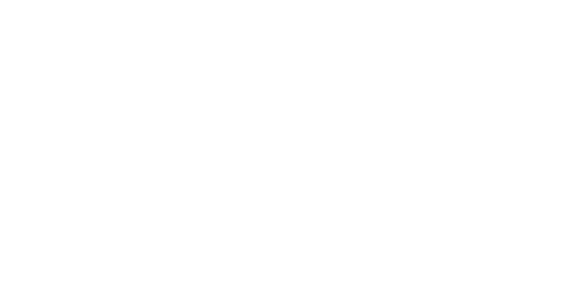
Up to 64% Lower Returns Processing Cost
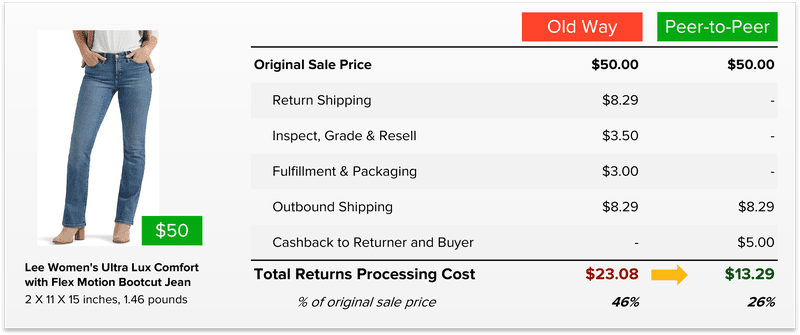