Warehouse KPIs: Measurement, Implementation, and Optimization

Last updated on March 5, 2025
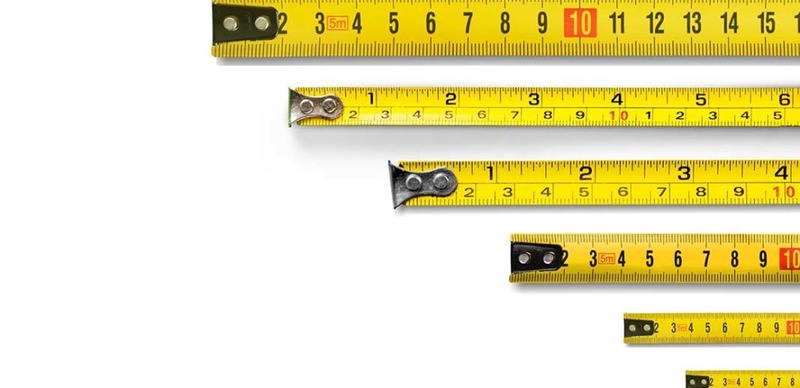
Warehouse Key Performance Indicators (KPIs) are essential metrics that drive operational excellence in logistics and supply chain management. These quantifiable measurements help warehouse managers track performance, identify inefficiencies, and make data-driven decisions to enhance productivity and profitability.
What Are KPIs and Their Value in Warehouse Management
Key Performance Indicators are specific, measurable values that demonstrate how effectively a company is achieving its business objectives. In warehouse operations, KPIs provide insights into operational efficiency, resource utilization, and overall performance.
The value of warehouse KPIs extends beyond simple measurement. They:
- Establish clear performance standards and expectations
- Identify operational bottlenecks and inefficiencies
- Facilitate data-driven decision making
- Enable continuous improvement processes
- Support budget justification and resource allocation
- Align warehouse operations with broader business goals
- Provide objective criteria for employee performance evaluation
KPIs transform reporting from a reactive to a proactive operation, where performance trends can be analyzed and addressed before they impact the bottom line.
How to Measure Warehouse KPIs
Effective KPI measurement requires a structured approach:
- Define Clear Objectives: Identify what you want to achieve in your warehouse operation. Objectives should align with overall business goals and be specific, measurable, achievable, relevant, and time-bound (SMART).
- Select Relevant KPIs: Choose metrics that directly relate to your defined objectives. Too many KPIs can dilute focus, so prioritize those most impactful to your operation.
- Establish Baselines: Measure current performance to establish a starting point against which future performance can be compared.
- Set Realistic Targets: Determine achievable performance targets based on historical data, industry benchmarks, and business requirements.
- Implement Measurement Systems: Deploy appropriate technologies and processes to collect accurate data, whether through warehouse management systems (WMS), barcode scanners, or manual tracking.
- Analyze Regularly: Review KPI data at consistent intervals to identify trends, anomalies, and improvement opportunities.
- Take Action: Implement changes based on KPI insights and track the impact of these changes on performance metrics.
- Refine and Adjust: Periodically reassess KPI relevance and modify your measurement approach as warehouse operations evolve.
Warehouse KPIs by Type
There are many different KPIs that can apply to warehousing. Here are several different types of KPIs, with some specific KPI examples and formulas to calculate them.
Understanding Inventory Management KPIs
Inventory management key performance indicators (KPIs) are critical metrics that provide warehouse and logistics managers with essential insights into the efficiency, accuracy, and financial performance of their inventory operations. These quantitative measurements serve as diagnostic tools that transform raw operational data into actionable intelligence, enabling businesses to optimize stock levels, reduce costs, improve customer satisfaction, and make data-driven strategic decisions. By tracking specific indicators across various stages of inventory management—from receiving and storage to order fulfillment—organizations can identify bottlenecks, minimize waste, and create more responsive and lean supply chain processes.
Inventory Management KPIs
KPI |
Purpose |
Formula |
Ideal Target |
---|---|---|---|
Inventory Accuracy |
Measures precision of inventory record-keeping |
(Accurate Inventory Records ÷ Total Inventory Records) × 100% |
≥ 98% |
Inventory Turnover Rate |
Indicates how quickly inventory is sold and replaced |
Cost of Goods Sold ÷ Average Inventory Value |
4-6 times per year |
Days on Hand |
Average duration inventory is held before sale |
(Average Inventory Value ÷ Cost of Goods Sold) × Number of Days in Period |
Minimize while maintaining service levels |
Carrying Cost of Inventory |
Percentage cost of holding inventory |
(Storage Costs + Capital Costs + Inventory Service Costs + Inventory Risk Costs) ÷ Total Inventory Value |
15-30% of inventory value |
Receiving KPIs
KPI |
Purpose |
Formula |
Ideal Target |
---|---|---|---|
Receiving Efficiency |
Measures units processed per labor hour |
Units Received ÷ Labor Hours Spent Receiving |
Maximize productivity |
Receiving Cycle Time |
Total time to process incoming shipments |
Time from Truck Arrival to Inventory Availability |
Minimize processing time |
Receiving Accuracy |
Percentage of orders received without errors |
(Correctly Received Orders ÷ Total Received Orders) × 100% |
≥ 99% |
Supplier On-Time Delivery |
Measures supplier delivery performance |
(On-Time Deliveries ÷ Total Deliveries) × 100% |
≥ 95% |
Putaway KPIs
KPI |
Purpose |
Formula |
Ideal Target |
---|---|---|---|
Putaway Accuracy |
Percentage of items placed in correct locations |
(Correctly Located Items ÷ Total Items Put Away) × 100% |
≥ 99% |
Putaway Cycle Time |
Time to transport items to storage locations |
Average Time from Receiving to Storage |
Minimize processing time |
Putaway Cost per Unit |
Average cost to place one unit in storage |
Total Putaway Costs ÷ Number of Units Put Away |
Minimize cost |
Order Management KPIs
KPI |
Purpose |
Formula |
Ideal Target |
---|---|---|---|
Order Picking Accuracy |
Percentage of orders picked without errors |
(Correctly Picked Orders ÷ Total Orders Picked) × 100% |
≥ 99.5% |
Order Picking Productivity |
Measures workforce picking efficiency |
Units Picked ÷ Labor Hours Spent Picking |
Maximize productivity |
Perfect Order Rate |
Comprehensive performance metric |
(Orders Delivered Complete, Accurate, On-Time, and Undamaged ÷ Total Orders) × 100% |
≥ 95% |
Order Cycle Time |
Total order processing time |
Average Time from Order Receipt to Shipment |
Minimize processing time |
Fill Rate |
Percentage of order items fulfilled on first shipment |
(Number of Items Shipped ÷ Number of Items Ordered) × 100% |
≥ 95% |
Safety KPIs
KPI |
Purpose |
Formula |
Ideal Target |
---|---|---|---|
Incident Rate |
Safety incidents per 100 employee-years |
(Number of Recordable Incidents × 200,000) ÷ Total Hours Worked |
Minimize |
Lost Time Injury Frequency Rate |
Injuries resulting in lost work time |
(Number of Lost Time Injuries × 1,000,000) ÷ Total Hours Worked |
Zero incidents |
Safety Training Compliance |
Percentage of employees with current safety training |
(Employees with Up-to-Date Safety Training ÷ Total Employees) × 100% |
100% |
Near Miss Reporting |
Potential incidents without injury or damage |
Number of Near Misses Reported |
Encourage reporting |
Challenges in Using Warehouse KPIs
Implementing key performance indicators (KPIs) in warehouse management can significantly impact operational effectiveness. Data quality emerges as a critical first hurdle, as the accuracy and completeness of performance metrics fundamentally depend on reliable information collection. Inaccurate or incomplete data can lead to misleading KPI values, causing management to make strategic decisions based on flawed insights. For instance, a warehouse might appear to be performing efficiently according to its metrics, when in reality, underlying data collection issues are masking critical operational inefficiencies.
The risk of over-measurement further complicates KPI implementation, creating a potential scenario of information paralysis. When organizations attempt to track an excessive number of metrics, they inadvertently dilute their focus and create unnecessary complexity in performance management. This approach can overwhelm warehouse managers and staff, making it difficult to concentrate on the most critical performance indicators that truly drive operational excellence. The key lies in strategic selection; choosing a focused set of KPIs that provide meaningful insights without causing cognitive overload or distracting from core operational objectives.
Organizational dynamics introduce another layer of complexity in KPI management, particularly through misaligned incentives and potential employee resistance. Performance metrics can sometimes create unintended consequences by encouraging behaviors that might optimize one aspect of performance while undermining another. For example, a KPI emphasizing order processing speed might inadvertently compromise order accuracy, or metrics rewarding individual productivity could potentially discourage collaborative teamwork. Moreover, employees may perceive performance measurement as a threatening surveillance mechanism rather than a tool for continuous improvement, leading to potential resistance and reduced engagement.
The financial and operational investment required for sophisticated KPI implementation presents a significant challenge for many warehouses. Establishing robust measurement systems demands substantial investments in technology infrastructure, data collection tools, and comprehensive staff training programs. These costs can be particularly prohibitive for smaller organizations with limited resources. Additionally, KPIs are not static constructs but dynamic tools that require continuous refinement. Context sensitivity demands periodic reassessment and adjustment of metrics to account for seasonal variations, evolving business strategies, technological advancements, and changing market conditions. Successful KPI implementation thus requires not just initial investment, but ongoing commitment to adaptability, technological integration, and organizational learning.
Tools for Measuring KPIs
Modern warehouse operations utilize various tools to measure and track KPIs:
- Warehouse Management Systems (WMS): Comprehensive software solutions that manage inventory, track orders, and generate KPI reports.
- Enterprise Resource Planning (ERP) Systems: Integrate warehouse data with broader business metrics for holistic performance measurement.
- Business Intelligence (BI) Platforms: Transform raw data into actionable insights through visualization and analytical capabilities.
- IoT Sensors and RFID: Provide real-time tracking of inventory movement and equipment utilization.
- Barcode and QR Code Systems: Enable accurate data capture for inventory and order processing.
- Labor Management Systems (LMS): Track individual and team productivity metrics.
- Data Dashboards: Present KPI information visually for quick decision-making.
Advanced Strategies and Tips for Using KPIs
Once KPIs are established, there are additional ways to leverage KPIs. First, predictive analytics leverage historical KPI data to forecast future performance trends and proactively address potential issues. Implement systems that provide immediate feedback on critical KPIs, allowing for rapid response to developing issues.
Remember that not all KPIs carry the same weight; ensure KPIs address multiple perspectives: financial, customer, internal processes, and learning/growth and implement tiered KPI structures where high-level metrics cascade down to operational-level indicators, creating alignment across the organization.
Finally, make KPIs collaborative; involve warehouse staff in KPI development to increase buy-in and ensure metrics are practical and relevant. Use friendly competition and recognition to drive KPI improvement among warehouse teams.
KPIs vs. Benchmarks
KPIs and benchmarks serve complementary purposes in warehouse management. KPI’s measure the business performance internally against itself, while benchmarks compare business performance to industry best practices.
Effective warehouse management requires both internal KPIs for operational control and external benchmarks for strategic positioning. While KPIs track progress toward specific operational goals, benchmarks provide context for how your performance compares to industry standards, helping identify competitive advantages or improvement opportunities.
When using benchmarks, consider industry segment, warehouse size, product type, and geographical location to ensure relevant comparisons. Sources for benchmark data include industry associations, consulting firms, and supply chain research organizations.
Conclusion
In conclusion, warehouse KPIs provide the quantitative foundation for data-driven management, operational excellence, and continuous improvement. When properly selected, measured, and analyzed, these metrics transform warehouse operations from cost centers to strategic assets that contribute significantly to organizational success.
Frequently Asked Questions
How do I Track Warehouse KPIs?
Each KPI has their own metric or formula. For example, inventory accuracy is measured by
Number of Errors / Total Inventory x 100%.
What are the Most Important Warehouse KPIs to Track?
There are many KPIs, and just tacking on KPIs doesn’t help. In general, Accuracy and Cost related KPIs are always helpful.
What is the Best Way to Monitor Warehouse KPIs?
Use Warehouse Management Systems (WMS) or Inventory Management Software to automatically track and analyze KPIs.
How Often Should I Review Warehouse KPIs?
KPIs should be reviewed weekly or monthly; KPIs should be used to correct and adjust before problems become major issues.
The Most Profitable Returns Solution
Ever Created
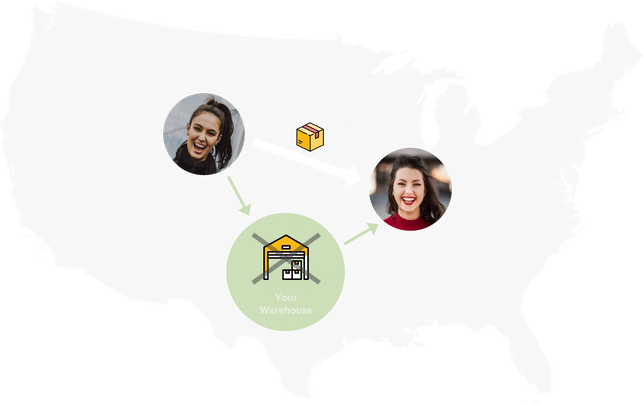