Essential WMS Features for Effective Warehouse Management

Last updated on April 15, 2025
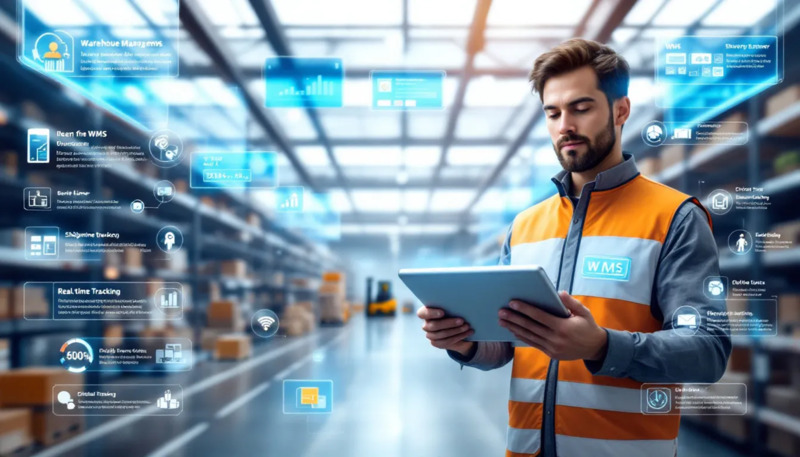
In this article
11 minutes
- Key Takeaways
- Understanding Warehouse Management Systems (WMS)
- Key Features of Inventory Management in WMS
- Warehouse Slotting & Location Management
- Inbound Receiving & Put-Away Optimization
- Multi-Channel Order Management
- Intelligent Shipping & Cost Optimization
- Automated Picking & Packing
- Efficient Returns Processing
- Seamless System Integrations
- Mobile-Enabled Warehouse Operations
- Advanced Analytics & Performance Insights
- Security Features
- Choosing the Right WMS for Your Business
- Summary
- Frequently Asked Questions
Looking for essential WMS features? Key functionalities like real-time inventory tracking, order management, and automation are the foundation to a successful solution. This article covers the top features you need in a Warehouse Management System.
Key Takeaways
- A WMS is the lifeblood of warehouse operations, automating inventory tracking, order processing, and fulfillment to enhance efficiency and reduce costs.
- Real-time inventory visibility and advanced reporting provide critical insights for better decision-making and operational optimization.
- Seamless system integration with ERP, CRM, and ecommerce platforms ensures scalability, adaptability, and efficiency which are essential for handling future growth and increased operational complexities.
- Optimized warehouse workflows, from location management to returns processing, minimize delays, reduce errors, and improve space utilization.
- Intelligent shipping and fulfillment automation streamline picking, packing, and shipping, cutting costs and improving order accuracy.
Understanding Warehouse Management Systems (WMS)
A Warehouse Management System (WMS) is warehouse management software designed to manage daily warehouse operations and inventory. Automating routine tasks such as inventory tracking and order processing, a WMS enhances operational transparency and efficiency. The implementation of a WMS not only optimizes warehouse operations but also significantly reduces waste and costs, improving labor management and relationships.
Real-time visibility into inventory is a standout feature of WMS, crucial for effective warehouse and supply chain management. This real-time data helps optimize operations, enhance efficiency, and improve forecasting for better decision-making. Additionally, data collection and process automation offered by WMS streamline operations from receiving to shipping, ensuring that every step is as efficient as possible.
The benefits of using a WMS extend beyond mere efficiency gains. Automating processes and providing real-time data, a WMS reduces operational costs and enhances transparency. This not only makes warehouse management more efficient but also sets the stage for a more agile and responsive supply chain. In today’s competitive market, the ability to quickly adapt to changes and optimize warehouse operations is a game-changer.
Key Features of Inventory Management in WMS
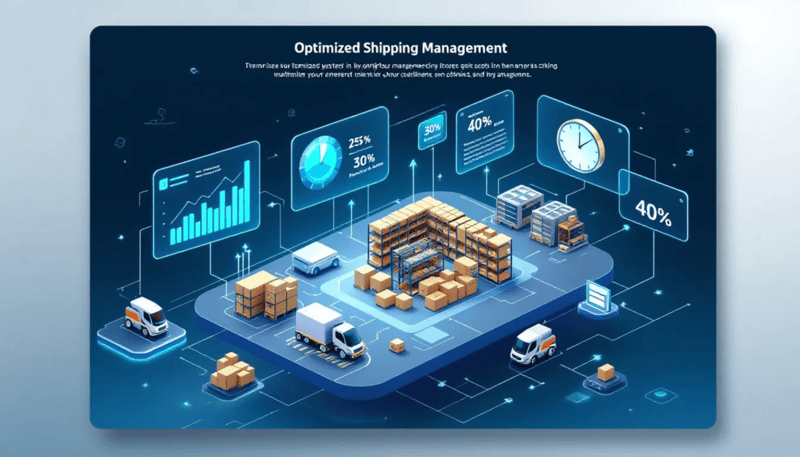
Inventory management is the backbone of any effective warehouse management system. A robust WMS offers real-time visibility across multiple locations, including items in transit and in stores. This ensures that warehouse managers always have accurate information about stock levels, helping to avoid the pitfalls of stockouts or overstocking. Real-time inventory visibility is a key feature that supports efficient warehouse management and timely order fulfillment.
Modern WMS platforms have essential features available for inventory tracking. These include barcode scanning and RFID technology for enhanced accuracy. These technologies enable precise inventory control, minimizing discrepancies and reducing the risk of errors. Barcode scanning and RFID are integral to streamlining inventory management, as they provide real-time data on inventory movement and location. Additionally, support for Stock Keeping Units (SKU) and detailed attribute logging further enhances inventory accuracy.
Automatic inventory allocation is another important feature of a WMS. This functionality ensures that inventory is efficiently allocated to various tasks such as orders and replenishments, optimizing warehouse operations. Maintaining precise stock levels and managing locations effectively, a WMS streamlines warehouse processes, simplifying the management of multiple warehouses and ensuring timely order fulfillment.
1. Warehouse Slotting & Location Management
Efficient warehouse location management is essential for businesses, especially with today’s need for rapid order fulfillment. Unique location IDs within a WMS simplify tracking and managing inventory across various warehouses or internal zones. This level of detail ensures that inventory control is maintained, and warehouse operations run smoothly. A WMS also:
- Optimizes storage space and dynamically slots goods based on relevant criteria such as rotation rate and seasonality.
- Enables warehouse layout optimization to reduce warehouse worker travel time.
- Warehouse layouts can be configured to adapt to specific business needs.
2. Inbound Receiving & Put-Away Optimization
The inbound receiving process is a critical aspect of warehouse management. A WMS provides visibility of upcoming deliveries, including delivery date and time, and size of delivery. This advanced notice allows warehouse managers to prepare for incoming shipments, ensuring that resources are allocated efficiently. Additionally, a WMS:
- Supports blind receipt and verifies incoming shipments.
- Confirms that all received products match the purchase orders.
- Optimize the put-away locations to help reduce travel time.
- Increases storage efficiency.
- Supports barcode scanning and RFID technology for ensuring that inventory is accurately tracked from the moment it enters the warehouse.
By streamlining these processes, a WMS enhances overall warehouse flow and improves efficiency, making it easier to manage daily warehouse operations.
3. Multi-Channel Order Management
Order management is a critical component of a WMS. Modern WMS platforms can handle various order inputs such as online stores and marketplaces, social commerce, CSV uploads, API/EDI connections, EPOS, and manual input. This capability allows businesses to manage orders from multiple channels through one platform, automating accuracy and speed.
- Real-time inventory management.
- Accurate tracking of product locations and order statuses.
- Multi-channel order management, processing, and tracking.
- Order data analytics and reporting.
The integration of WMS facilitates a seamless workflow, reducing order processing times significantly.
4. Intelligent Shipping & Cost Optimization
Shipping management is a central aspect of warehouse operations, and a WMS offers several features to optimize this process. A WMS should compare rates between couriers, automatically generate shipping labels, and integrate with shipping sortation technology. This automation increases shipping accuracy and timeliness, ensuring that orders are delivered promptly and correctly, at the lowest transportation cost.
- Automatic rate shopping and shipping label creation to select the most cost-effective carrier for each order.
- Load consolidation helps reduce shipping costs by grouping orders destined for the same location.
- Cross-docking functionality for the immediate shipping of incoming goods, bypassing traditional storage.
- Automated cartonization using AI to determine the best packaging size for each order and reduce dimensional weight costs.
These features collectively enhance the efficiency and cost-effectiveness of the shipping process, ensuring timely order fulfillment.
5. Automated Picking & Packing
Order picking and packing are crucial processes in warehouse management, and a WMS plays a significant role in streamlining these tasks. Order picking processes include specific order picking, bulk picking, and utilization of tote trolleys, all of which are optimized by WMS. Reducing human error and utilizing automation, a WMS enhances efficiency and improves order fulfillment.
- Double verification of picked items.
- Automatic generation of the packing paperwork.
Efficient picking and packing processes keep your customers happy by ensuring orders are delivered on time.
6. Efficient Returns Processing
A clear and efficient returns process is essential for effective warehouse management processes. A WMS manages returns by receiving and inspecting returned goods, classifying products, and handling re-stocking or refunds for goods that cannot be re-stocked. This ensures that the returns process is streamlined and efficient, reducing the impact on warehouse operations.
- Efficient processes for handling returns, including tracking, processing, and reintegrating returned products into inventory.
- Automating the creation of customer-specific shipping documents.
- Compliance with product-specific requirements to ensure proper conditioning for resale.
Advanced systems offering peer-to-peer returns entirely removes returns processing from the Seller’s responsibility, reducing the cost of reverse logistics by 60 – 70%!
7. Seamless System Integrations
Integration capabilities are critical for a WMS to function effectively within a business ecosystem. A robust WMS integrates with ERP, finance management systems, CRM, and open APIs for custom integration. This ensures a smooth connection with ERP systems, transportation management systems (TMS), and ecommerce platforms, facilitating seamless data exchange across logistics operations. Advanced tracking systems in WMS enable comprehensive visibility across the supply chain, informing better operational decisions.
8. Mobile-Enabled Warehouse Operations
Support for mobile devices is a significant advantage of modern WMS, providing real-time inventory tracking in the warehouse and enhancing operational efficiency. Mobile technology like barcode scanners enhances accuracy by providing real-time inventory levels at your fingertips.
This mobile accessibility minimizes reliance on manual processes, making daily warehouse operations more efficient and streamlined by facilitating quick order processing and shipping label generation directly from devices.
9. Advanced Analytics & Performance Insights
Advanced reporting and analytics are key features of a WMS, providing insights into on-time shipping, on-time delivery, inventory accuracy, and fulfillment cycle time.
- Real-time tracking allows for immediate monitoring of resource allocation and processing gaps and delays.
- GenAI integration assists with automating decisions based on patterns in historical data, warehouse layout, etc.
- Customizable reporting features allow businesses to derive actionable insights from key performance indicators.
These tools are necessary for tracking performance metrics such as average lead times, identifying bottlenecks, and finding opportunities for optimization.
10. Security Features
As warehouses become more digitized and interconnected, securing sensitive customer data and ensuring operational resilience are mission critical. A robust WMS must incorporate advanced security measures to protect against data breaches, unauthorized access, and system vulnerabilities. These security features not only safeguard valuable business and customer information but also ensure the system can scale securely as operations grow. Below are five essential security features every WMS must have to maintain data integrity, prevent breaches, and support a scalable, secure WMS environment.
- Role-Based Access Control (RBAC) – Restricts system access based on user roles, ensuring employees can only view and modify data relevant to their responsibilities.
- Data Encryption – Uses encryption (both in transit and at rest) to safeguard sensitive customer and operational data from unauthorized access.
- Multi-Factor Authentication (MFA) – Adds an extra layer of security by requiring multiple forms of verification before granting system access.
- Audit Logging & Monitoring – Tracks user activity, system changes, and access attempts to detect and respond to security threats proactively.
- Secure API & Third-Party Integrations – Ensures that data exchanges with ERP, TMS, and ecommerce platforms are protected through encrypted and authenticated API connections.
Choosing the Right WMS for Your Business
Selecting the right WMS can significantly enhance warehouse efficiency and improve overall productivity. Understanding your warehouse’s size and complexity is crucial for aligning a WMS with your specific business goals. One size doesn’t fit all; businesses should look for solutions with must-have features to meet their current and future demands. But suffice to say that a truly effective WMS must deliver the capabilities described above to drive warehouse efficiency, accuracy, and cost-effectiveness.
Don’t let outdated systems hold you back; upgrade to a modern WMS software and meet customer demand with precision and ease while transforming your warehouse into a hub of efficiency and productivity.
Summary
A Warehouse Management System (WMS) is an indispensable tool for modern warehouse operations. From inventory management and order processing to shipping and returns management, a WMS covers all the critical aspects of warehouse management. By providing real-time visibility, automating processes, and integrating with other systems, a WMS enhances efficiency, reduces costs, and improves customer satisfaction.
Choosing the right WMS involves considering factors such as scalability, integration capabilities, and security features. As businesses grow and evolve, a flexible and scalable WMS can adapt to changing needs, ensuring that warehouse operations remain efficient and effective. Embrace the power of a WMS and transform your warehouse into a high-performing, customer-centric operation.
Frequently Asked Questions
What are the key features of a Warehouse Management System (WMS)?
A good Warehouse Management System (WMS) offers real-time inventory visibility, effective order management, optimized order routing and shipping processes, and detailed reporting and analytics to keep your operations running smoothly. These features help improve efficiency and accuracy in your warehouse which protect the bottom line.
How does a WMS improve order picking and packing processes?
A WMS improves order picking and packing by optimizing the movements of operators and providing clear picking instructions through technologies like voice recognition and barcode scanners. This leads to faster and more efficient packing with automated cartonization for optimal packaging.
Why is integration important for a WMS?
Integration is key for a WMS because it allows smooth connections with various systems like ERP and e-commerce platforms, leading to better data exchange and overall operational efficiency. This connectivity streamlines processes and enhances productivity.
What should businesses consider when choosing a WMS?
When choosing a WMS, businesses should prioritize scalability, integration capabilities, ease of use, automation features, and security to ensure it meets their needs effectively. These factors can make a big difference in optimizing operations.
How does mobile functionality benefit warehouse staff?
Mobile functionality helps warehouse staff by offering real-time inventory tracking and quick access to order processing, making operations smoother and less dependent on manual work. This ultimately boosts efficiency and saves time!
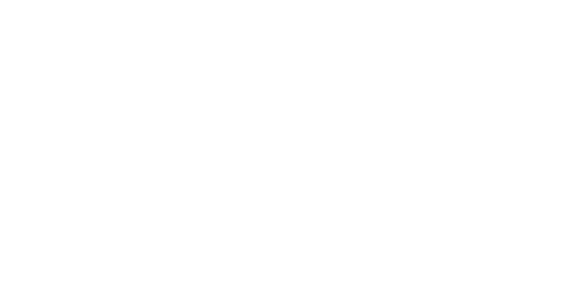
Up to 64% Lower Returns Processing Cost
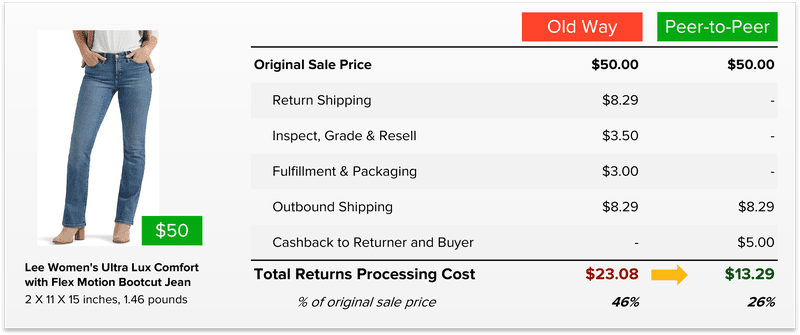